Centrifugal Barrel Finishers
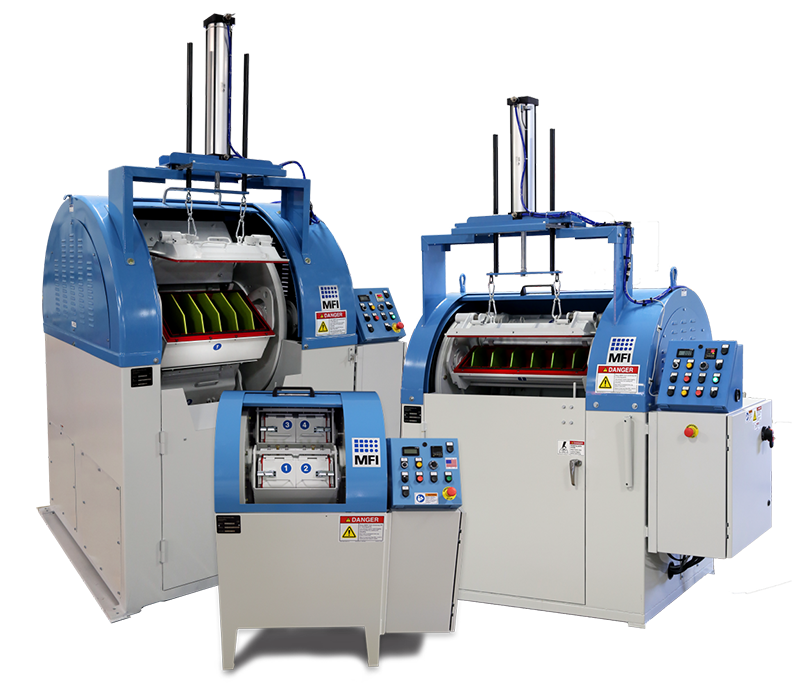
HZ-Series High Energy Centrifugal Barrel Finishing Machines
The HZ-Series Centrifugal Barrel Finishing Machines are our main expertise. These high-energy finishing machines feature four chambers that rotate around like a ferris wheel to create centrifugal force to finish and polish parts. They are the fastest and most economical form of tumble finishing equipment available. A wide range of industries utlilize these centrifugal barrel tumblers to polish, deburr, and deflash a variety of metal and non-metal components. From aerospace jet engine blades to medical implants, our HZ-Series centrifugal barrel tumblers are a versatile and reliable solution for achieving a cost-effective finishing result. What sets MFI apart when compared to other tumbling manufacturers is our support and experience with utilizing this type of equipment.
Benefits
- Reduce handwork and manual labor
- Easy to keep parts separated
- Quieter operation
- Achieve an isotropic mirror-like finish that is impossible to achieve by hand
- Short cycle times for faster turnaround and higher productivity
Available HZ-Series Models
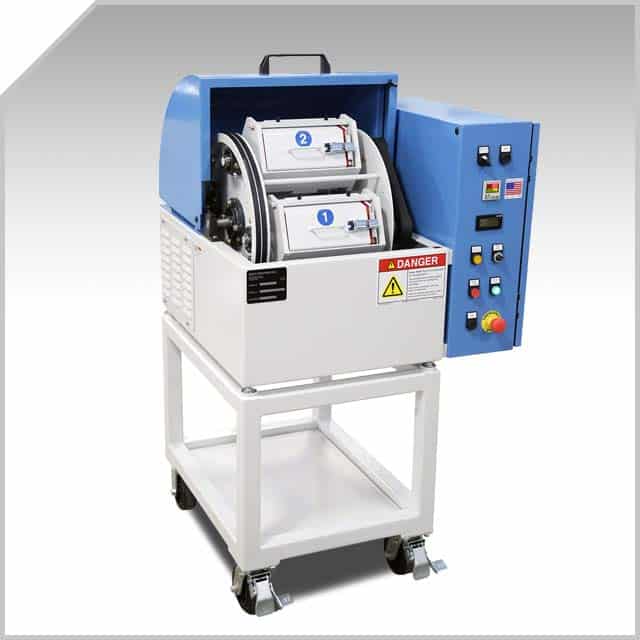
HZ-12
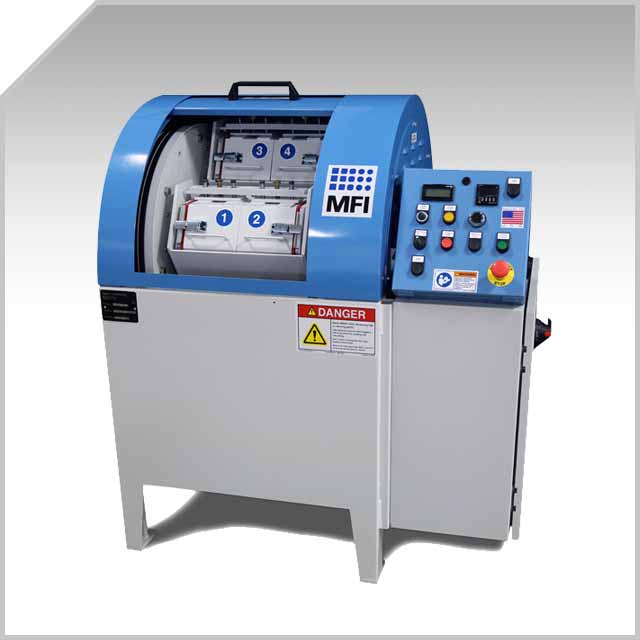
HZ-40
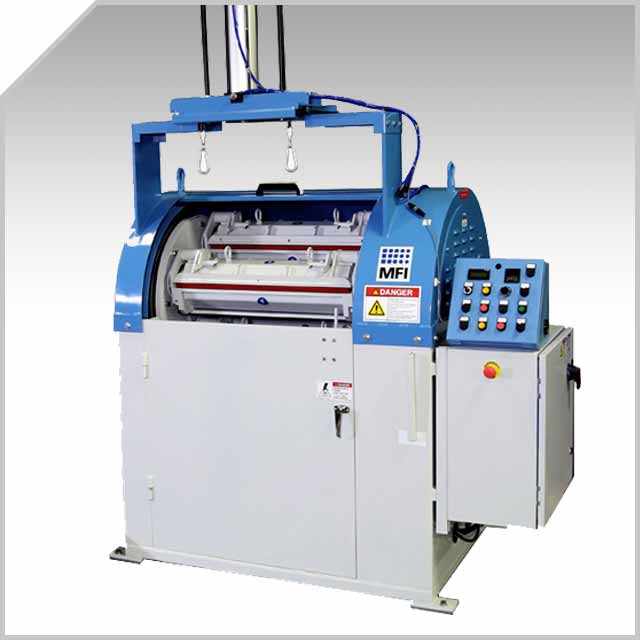
HZ-60
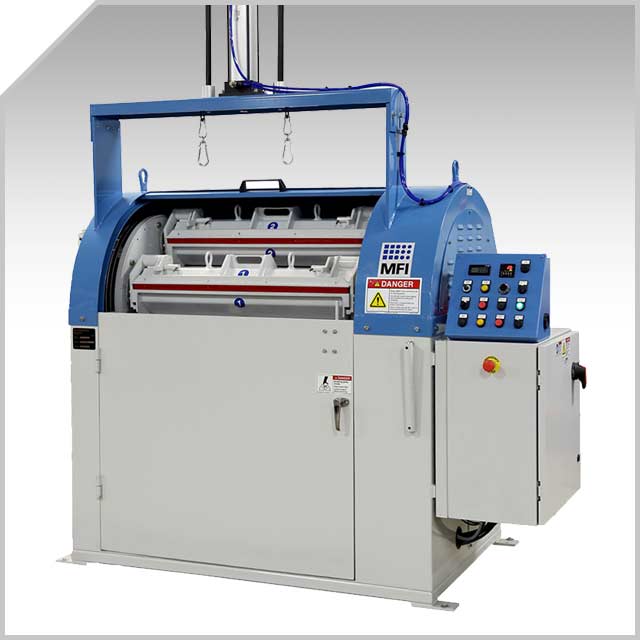
HZ-85
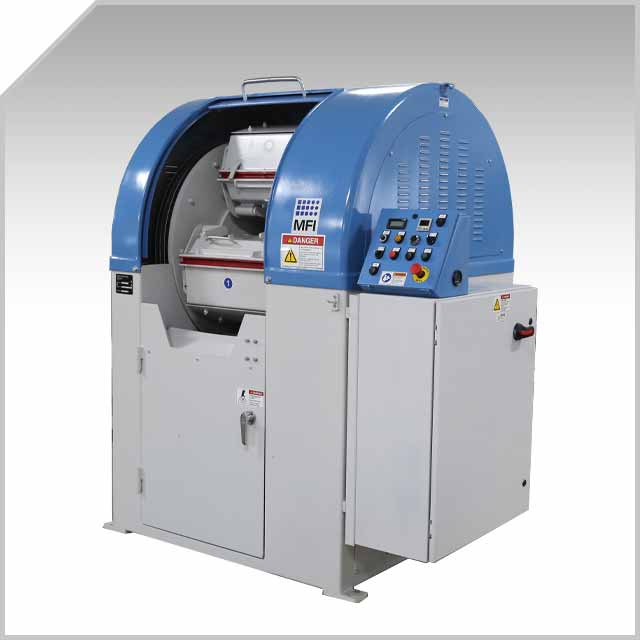
HZ-120
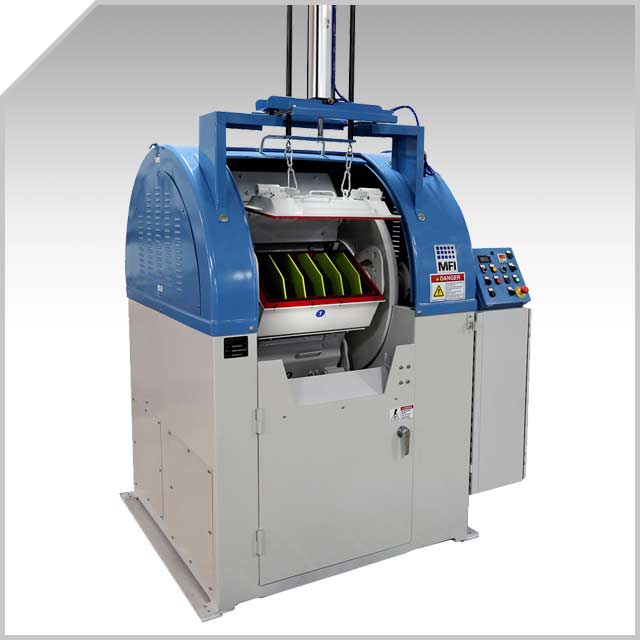
HZ-160
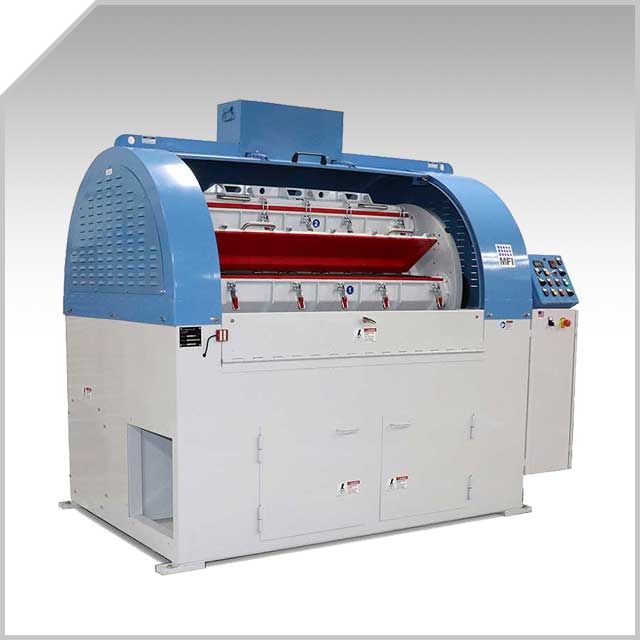
HZ-175
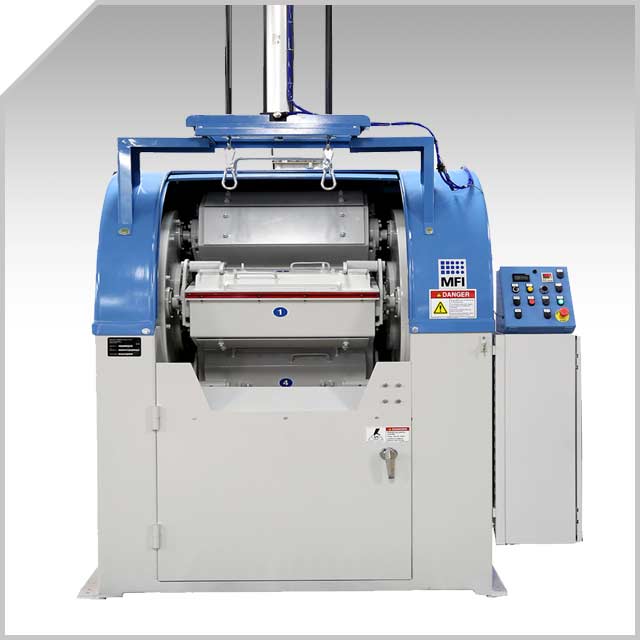
HZ-220
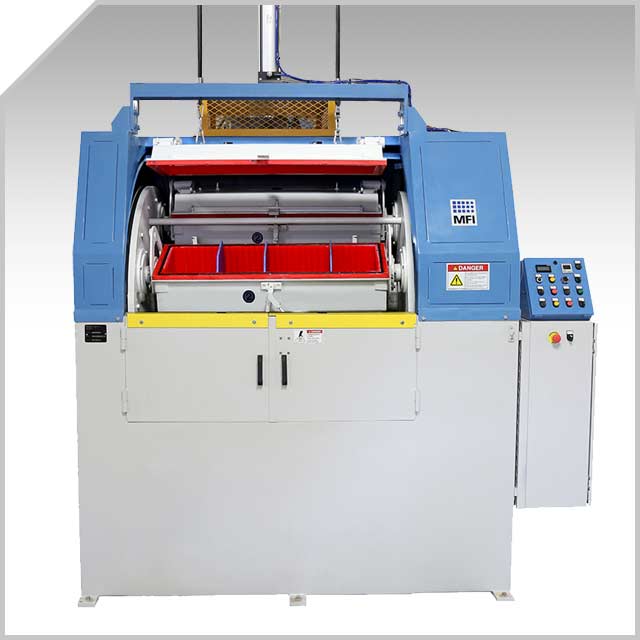
HZ-330
The Benefits of Centrifugal Barrel Finishing Machines
Reduce handwork & manual labor
Easy to keep parts separated
No tooling required
Quieter operation
Achieve a mirror-like finish
Short cycle times
Range of finishing capabilities
What is High-energy Centrifugal Barrel Finishing?
How does Centrifugal Barrel Tumbling Work?
As the centrifugal barrel finishing machine rotates, the barrels spin around the turret in a planetary motion, creating a sliding force inside the barrel. This motion generates high levels of friction and pressure between the abrasive media and parts and causes them to contact each other in random or isotropic directions. This results in an efficient process that removes burrs, polishes surfaces, and produces uniform finishes that are consistent across the entire part surface – also known as an isotropic finish.
Animation from DualSPHysics
HZ-Series: Max Part Size Chart
You can always reach out to our team if you need assistance determining what model of centrifugal barrel tumbler is right for your operation or production volume.
History of Centrifugal Barrel Tumbling or “Harperizing”
HZ-Series: Barrel Comparisons
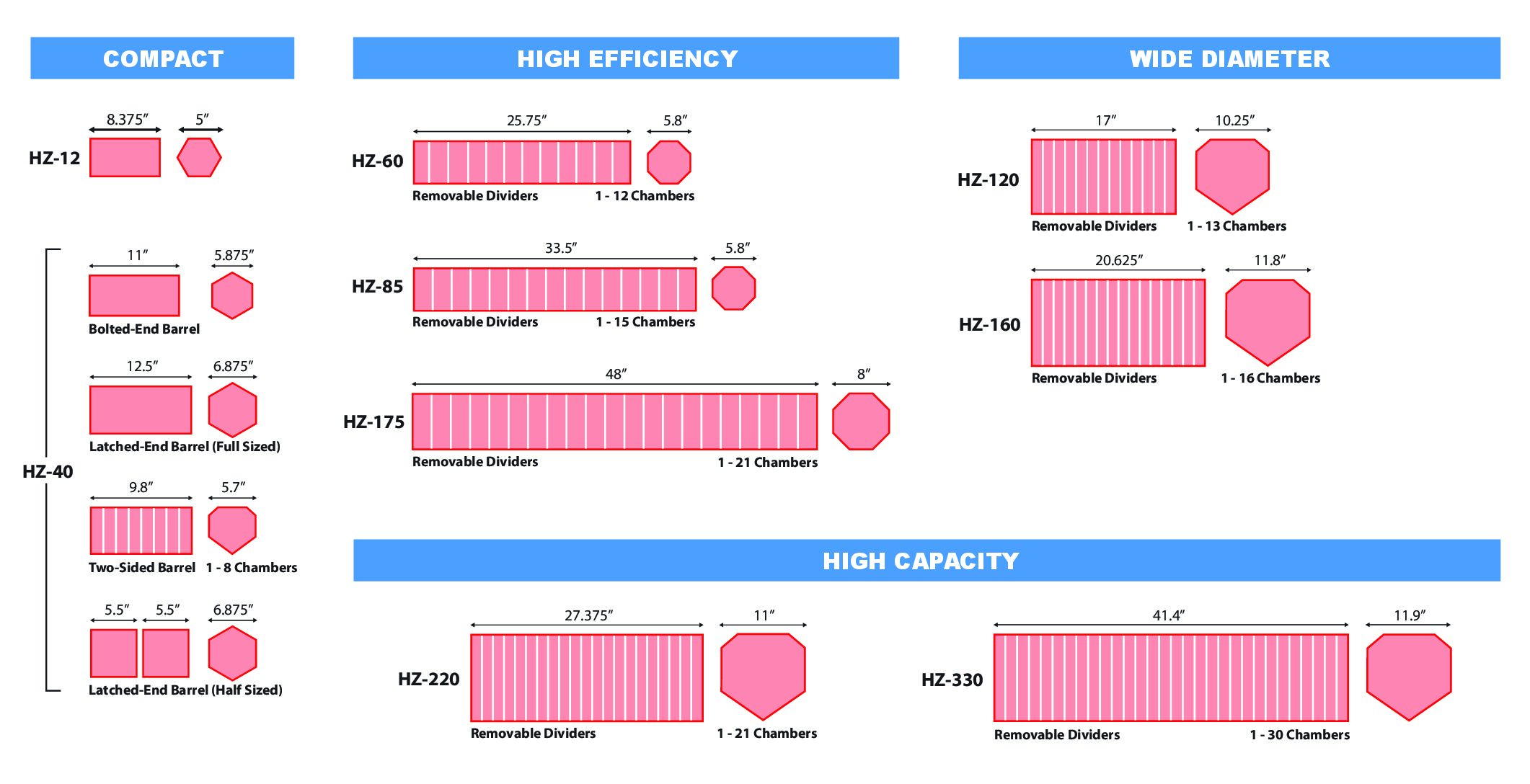