Knife Industry
Mass Finishing Solutions for the Knife Industry
At Mass Finishing Inc. (MFI), we’ve been providing high-quality finishing and polishing solutions for over two decades. Our High-Energy Centrifugal Barrel Finishing Machines provide a fast, efficient, and environmentally friendly solution for knife polishing and deburring. MFI works with custom and production knife makers around the world to provide unique matte and stonewashed finishes along with mirror polishes on blades. In a matter of minutes, customers take blades from their machining or heat-treating process and put them into our HZ-Series machines and have blades and other knife components ready for assembly. MFI processes are free of hazardous and expensive accelerated chemicals. We rely simply on the intense physical force of the machine.
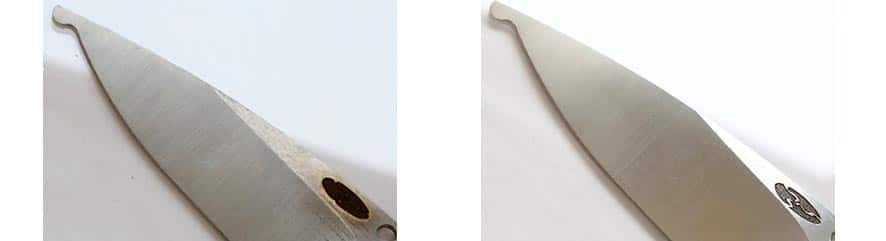
Common Parts:
Knives
Blades
Guards
Sheaths
Locking Mechanisms
Handles
Ready to Send Your Sample Parts?
Running samples in our lab is the best first step in determining the right equipment and process for your part. We process most samples within a week, depending on the number of samples we’re currently working on.
Recommended Knife Finishing Equipment: HZ-Series
When it comes to knife finishing and polishing, our High-Energy HZ-Series Centrifugal Barrel Finishing machines are the top choice of most customers in the Knife Industry. Our HZ-series machines offer efficient and repeatable processes for deburring Knife parts and achieving a variety of different finishes. Whether you want to remove burrs, create a matte or stonewash finish, or achieve a mirror polish, our HZ-Series machines can do it all.
Som of our most popular HZ-Series machines, such as the HZ-40, HZ-60, and HZ-85 each offer different blade capacity and can accommodate blades up to 33 inches long. Barrel dividers can be purchased to keep parts separated in individual compartments to eliminate the risk of part-on-part damage.
Benefits
-
Eliminate handwork
-
Reduced labor costs and production time
-
Remove machine lines
-
Create unique matte, stonewash, or mirror-like finishes
-
Finish multiple parts simultaneously
-
Improved part durability and corrosion resistance
-
Create an isotropic finish (even finish in all directions)
Knife Manufacturing Industry Average Process Times
Light Edge Break/Deburr
10 – 20 minutes
Rough Grind/Deburr
20 – 30 minutes
Full Polish from Raw Part
30 – 60 minutes
* Process times vary depending on the surface roughness.
Popular Equipment for the Knife Industry
The following models tend to be the most popular choices for those in the Knife Industry. The right model for your application will depend upon your specific part size, your production volume, and your finishing requirements. A full list of available equipment can be found on the equipment page.
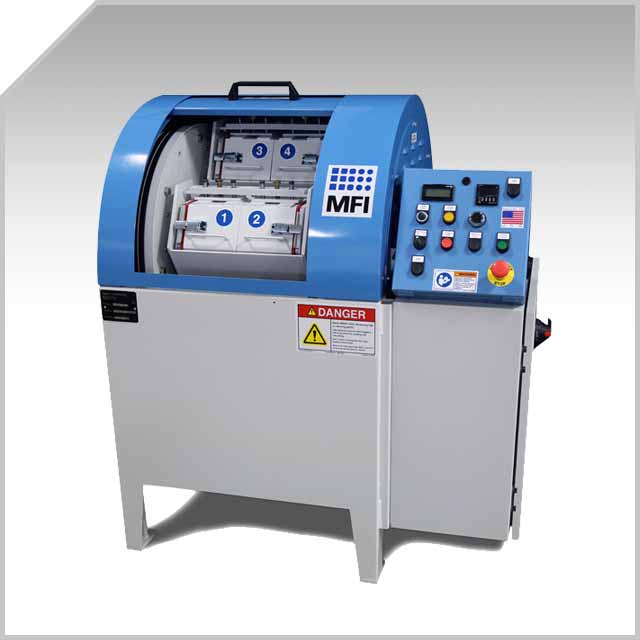
HZ-40
Compact machine. Versatile with 4 different barrel options.
Machine Type: Entry Level
Max Part Size: 11″ L x 5.5″ D
Barrel Dimensions: 12.5″ L x 6.75″ D
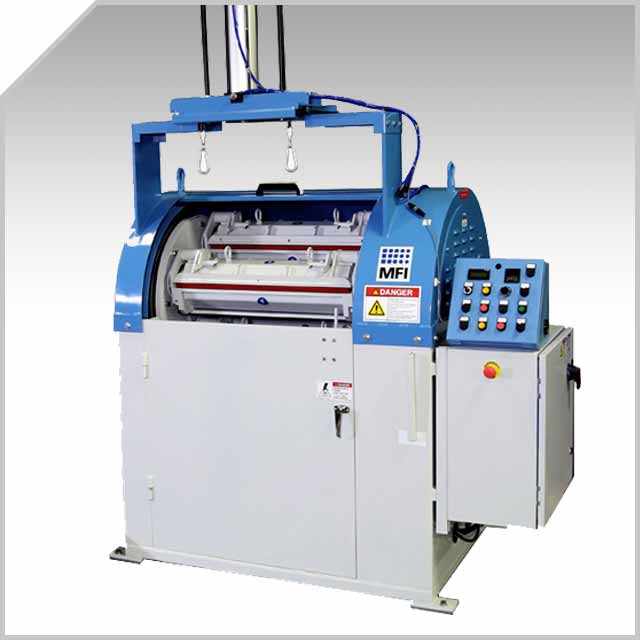
HZ-60
Full-size machine for larger production volume and part sizes.
Machine Type: High Efficiency
Max Part Size: 24″ L x 5.5″ D
Barrel Dimensions: 25.75″ L x 6″ D
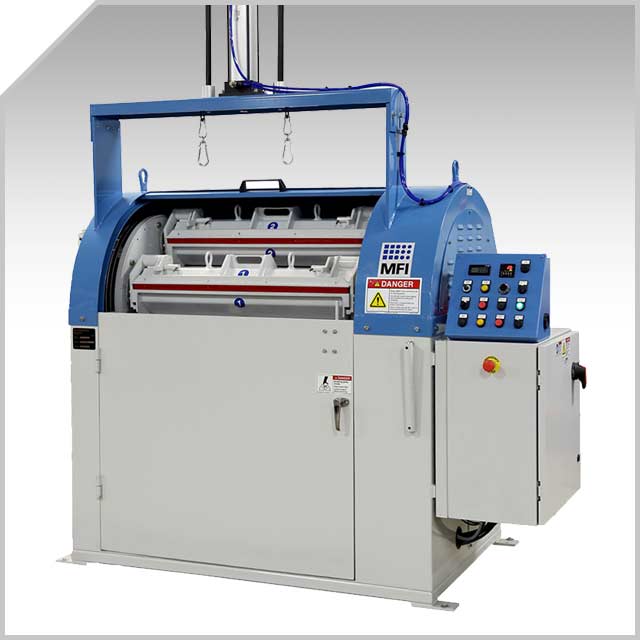
HZ-85
Full-size machine with even larger barrel capacity for greater production volume and part length.
Machine Type: High Efficiency
Max Part Size: 34″ L x 5.5″ D
Barrel Dimensions: 33.5″ L x 6″ D
Not sure what HZ-Series is right for you? You can view our Max Part Size Chart to see what model is best equipped to handle your part size and production volume.
Knife Sample Parts
Common Materials: Hardened Steel, Titanium, Aluminum, Stainless
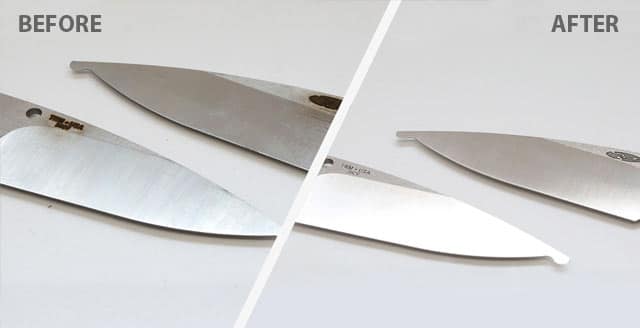
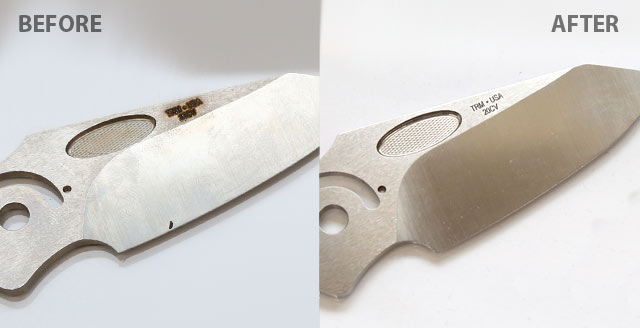
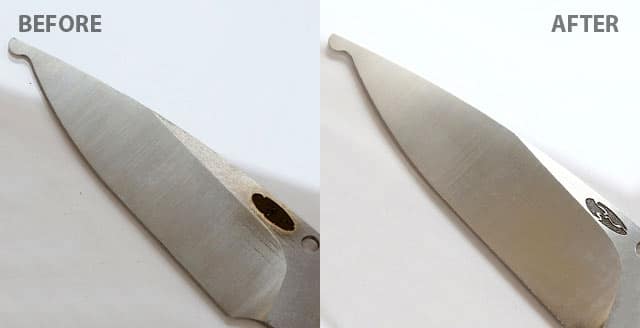
Enhance Your Mass Finishing Process with the Right Media Selection
Media is an essential component in the finishing process and is required for the proper operation of any Mass Finishing equipment. Finishing media is carefully selected based on its composition, shape, size, and performance to optimize the efficiency and effectiveness of the finishing process.
In addition to the wide variety of media and liquid and powder compounds in our Media Store, we also manufacture our own corn cob blends at our manufacturing facility in Howard Lake, MN.
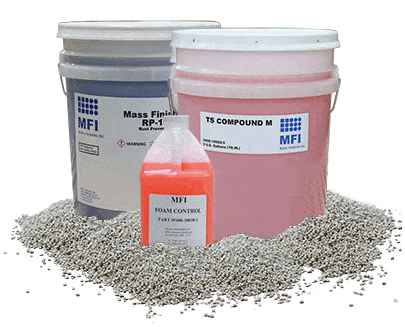
Achieve Perfect Knife Finishing