Aerospace Industry
Mass Finishing Solutions for the Aerospace Industry
At Mass Finishing Inc. (MFI), we’ve been providing high-quality aerospace finishing and polishing solutions for over two decades. Our High-Energy Centrifugal Barrel Finishing Machines remove machine lines, break sharp edges, stress-relieve, and add a mirror finish to a variety of extremely sensitive aerospace parts. We have successfully tested hundreds of aerospace parts, from jet engine blades to airplane engine parts, and have worked with industry leaders like Rolls Royce and GE to develop efficient and repeatable processes for deburring aerospace parts and achieving a variety of different finishes.
Common Parts:
Turbine Blades
Engine Components
Valves
Manifolds
Motor Housings
Fasteners
Instrument Components
Cosmetic Functional Parts
Ready to Send Your Sample Parts?
Running samples in our lab is the best first step in determining the right equipment and process for your part. We process most samples within a week, depending on the number of samples we’re currently working on.
Recommended Aerospace Finishing Equipment: HZ-Series
Most customers in the aerospace industry choose our High-Energy HZ-Series Centrifugal Barrel Finishing machines for their aerospace finishing and polishing applications. Our HZ-series machines are ideal for finishing critical parts like turbine blades in a one or two-step process. After tumbling, the blades are stress relieved and completely free of burrs and imperfections.
With our equipment, handwork is eliminated, allowing aerospace manufacturers to implement an aerospace surface finishing process that is efficient and repeatable.
Benefits
- Eliminate handwork
- Reduced labor costs and production time
- Remove machine lines and break sharp edges
- Stress-relieve parts, ensuring part longevity and durability
- Achieve a mirror-like finish on delicate parts
- Ensure consistent aerospace surface finishing
- Polish multiple parts simultaneously
Aerospace Industry Average
Process Times
Light Edge Break/Deburr
5 – 20 minutes
Rough Grind/Deburr
20 – 60 minutes
Full Polish from Raw Part
30 – 90 minutes
* Process times vary depending on the starting surface roughness.
Popular Equipment for the Aerospace Industry
The following models tend to be the most popular choices for those in the Aerospace Industry. The right model for your application will depend upon your specific part size, your production volume, and your finishing requirements. A full list of available equipment can be found on the equipment page.
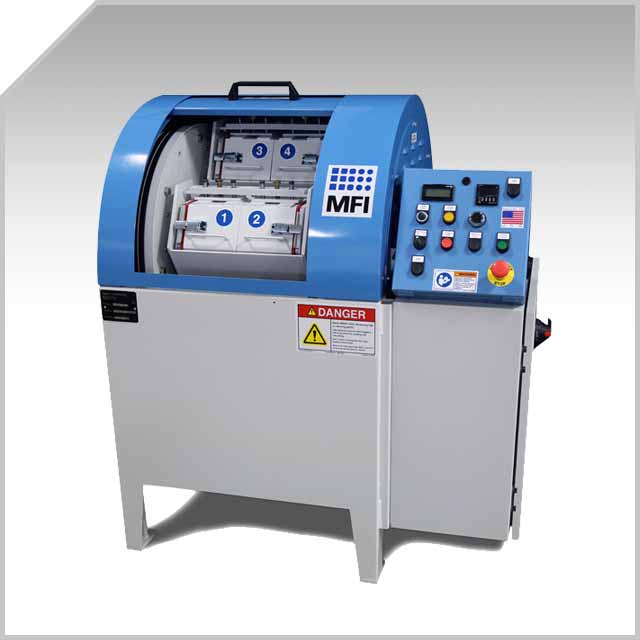
HZ-40
Compact machine with removable barrels. Ideal for smaller aerospace parts.
Machine Type: Entry Level
Max Part Size: 11″ L x 5.5″ D
Barrel Dimensions: 12.5″ L x 6.75″ D
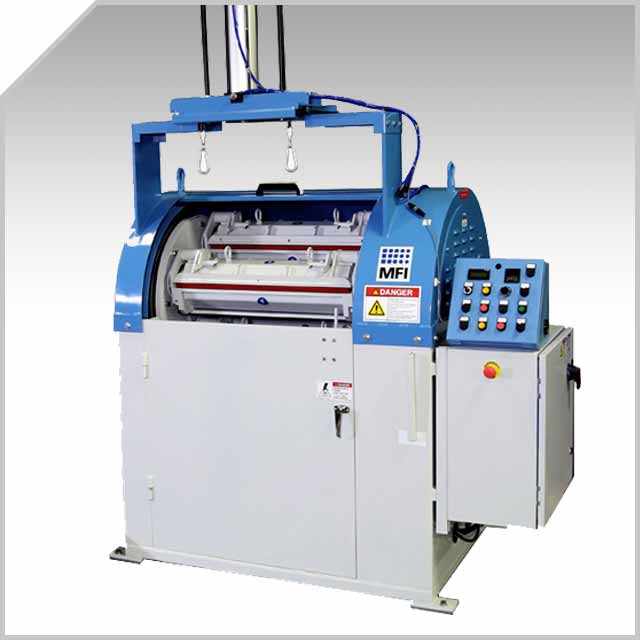
HZ-60
Full-size machine for larger production volume and part sizes.
Machine Type: High Efficiency
Max Part Size: 24″ L x 5.5″ D
Barrel Dimensions: 25.75″ L x 6″ D
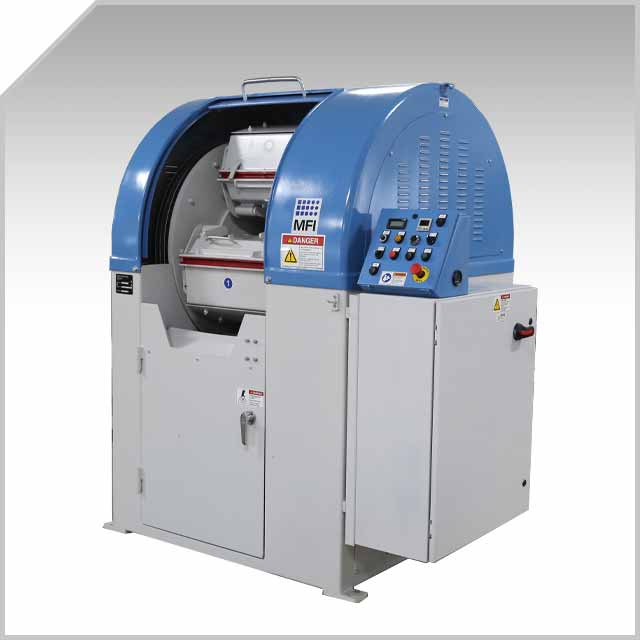
HZ-120
Full-size machine with a wider diameter barrel for larger parts.
Machine Type: Wide Diameter
Max Part Size: 16″ L x 9.5″ D
Barrel Dimensions: 17.25″ L x 10.25″ D
Not sure what HZ-Series is right for you? You can view our Max Part Size Chart to see what model is best equipped to handle your part size and production volume.
Aerospace Sample Parts
Common Materials: Titanium, Aluminum, Inconel, Nitinol, Plastics, and Hardened Steel
Enhance Your Mass Finishing Process with the Right Media Selection
Media is an essential component in the finishing process and is required for the proper operation of any Mass Finishing equipment. Finishing media is carefully selected based on its composition, shape, size, and performance to optimize the efficiency and effectiveness of the finishing process.
In addition to the wide variety of media and liquid and powder compounds in our Media Store, we also manufacture our own corn cob blends at our manufacturing facility in Howard Lake, MN.
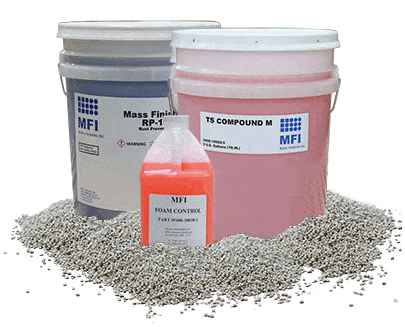
Achieve a Smoother Finish on Aerospace Parts