What is a Harperizer?
A harperizer is a high-energy finishing machine used in the surface finishing industry. It is known for its effective deburring, polishing, and finishing capabilities. Developed by the Harper company in the 1960s, harperizers use centrifugal force through the process of centrifugal barrel tumbling to create an effective and consistent finish on a variety of parts and materials.
Although no longer produced by Harper, the same centrifugal barrel tumbling technology used in the original harperizer is now utilized in modern-day centrifugal barrel tumbling machines such as Mass Finishing Inc.’s (MFI) HZ-Series Centrifugal Barrel Finishing Machines.
How Do Harperizers Work?
The original harperizer utilized a 4:1 barrel-to-turret ratio. Once filled with a mixture of parts, water, compound, and media, the barrels are locked. As the barrels start to rotate, they spin at high speeds. This rotation generates significant centrifugal force, hence producing high levels of friction and pressure between the abrasive media and parts. This, in turn, leads to efficient finishing processes.
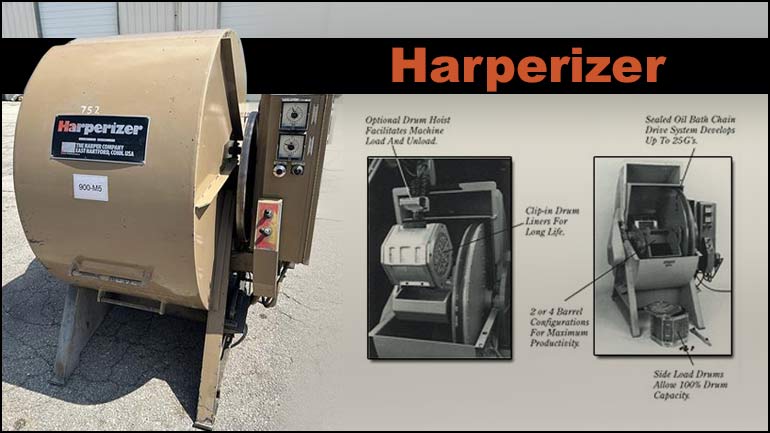
From Past to Present: The Evolution of Harperizers
In the realm of surface finishing, the term “harperizer” has long been synonymous with innovation and superior quality. For several decades, harperizers set the standard in surface finishing with their quick and efficient material removal. In fact, many industries such as aerospace and automotive still call-out in their finishing specifications that their parts need to be “harperized” or need to undergo finishing in a harperizer.
However, after Harper’s patent expired in the 1980’s, competitors like Timesavers, Tipton, Drehr Corporation, and NDI introduced machines with a 1:1 barrel-to-turret ratio. This challenged Harper’s hold over the market with more affordable and easier-to-operate equipment.
Known as centrifugal barrel tumblers, these competitors’ mass finishing machines drew inspiration from Korean designs. And incorporated a 1:1 barrel-to-turret ratio (meaning every time the turret rotated, the barrel’s counter rotated once). By switching to a 1:1 ratio versus the original 4:1, these finishing machines were able to generate higher energy, and therefore speed up the finishing process even further.
MFI’s Innovations in Harperizer Technology
Over the last 29 years, MFI has enhanced the original harperizer design by incorporating features like easier operation, faster processing, and improved safety against part-on-part damage. Our HZ-Series Centrifugal Barrel Tumblers reflect these advancements, offering nine stock sizes of equipment, designed to accommodate various parts and production volumes.
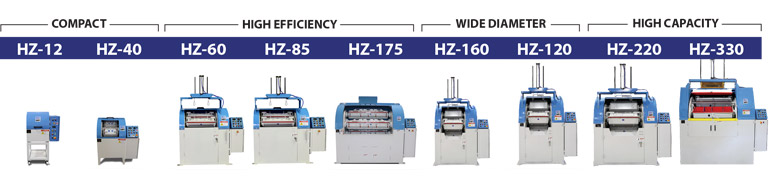
Key Difference in Machine Design: Then vs. Now
Barrel to Turret Ratio: As previously mentioned, the original harperizers had a 4:1 barrel-to-turret ratio. Whereas MFI’s centrifugal barrel machines boast a 1:1 ratio, resulting in greater energy efficiency and faster processing.
Ease of Operation: The original harperizers had a much bulkier design, were very cumbersome to run and hard to operate. MFI’s centrifugal barrel machines have been upgraded over the years, boasting a more streamlined and operator-friendly design.
MFI’s HZ-Series tumblers have updated controls, barrels, and offer a media separation and return system. This makes loading and unloading media and parts much easier.
No Part-On-Part Impingement: Traditional harperizers lacked separation features, making it hard to prevent part-on-part damage. MFI’s machines incorporate removable barrel dividers for better part separation.
Cost Efficiency: While the original harperizers were pioneers in the field, they were also expensive. Today’s centrifugal barrel equipment is more affordable while maintaining high-quality finishing capabilities.
Conclusion
As we look to the future, Mass Finishing Inc. continues to lead in the evolution of surface finishing technologies with its state-of-the-art harperizers.
Interested in experiencing the cutting-edge capabilities of our machines, or wish to learn more about their specifications? We encourage you to visit our HZ-Series product page, send in parts for free sample parts testing, or discussing your application with a member of the MFI team.