In the realm of medical device finishing, precision and quality are non-negotiable. At Mass Finishing, Inc. (MFI), we specialize in providing superior medical finishing systems via our high-energy centrifugal barrel tumbling equipment. Our medical parts finishing process creates an isotropic finish on parts, ensuring that medical devices meet stringent industry standards, contributing to safer and more effective healthcare outcomes.
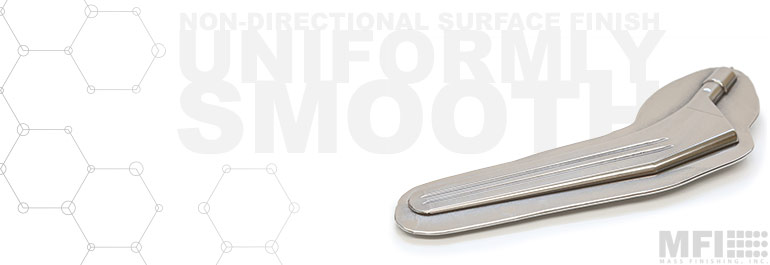
The Role of Isotropic Finishing in Medical Applications
Isotropic finishing stands out as a pivotal technique in medical device finishing. With its ability to create a uniformly smooth and non-directional surface finish, this process enhances the quality of complex medical devices, such as implants and surgical tools, by ensuring uniform and smooth surfaces.
MFI’s advanced isotropic finishing techniques are also pivotal in reducing risks associated with surgery, such as minimizing plaque buildup on implants, ultimately leading to improved patient outcomes.
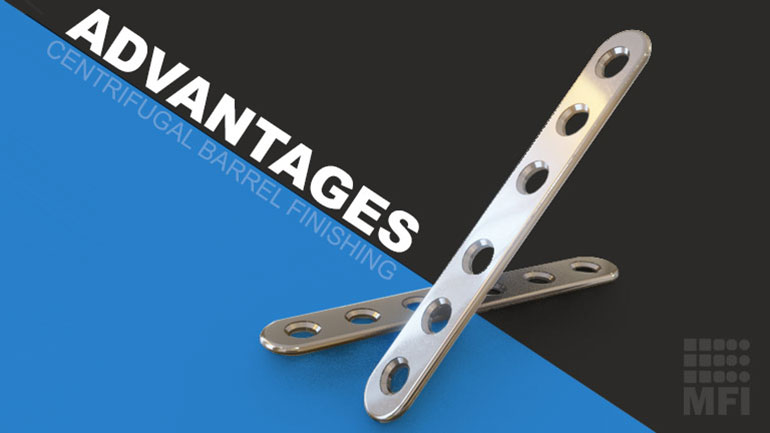
Advantages of Centrifugal Barrel Finishing in Medical Device Finishing
MFI’s High-Energy Centrifugal Barrel Tumbling Machines are at the forefront of metal finishing for medical applications. These systems offer multiple benefits including:
- Enhanced surface quality
- No part-on-part damage
- Reduced processing times
- Diverse material compatibility.
Let’s dive further into each of these benefits.
Enhanced Surface Quality
In the world of medical device finishing, the demand for varied surface qualities is as diverse as the devices themselves. At MFI, we understand this variety and tailor our processes to meet our customers’ specific needs. Often times, clients are seeking for either a high-polish finish, characterized by low surface roughness (Ra), or a matte finish, depending on the application.
For example: Some bone plates require a smooth but non-reflective surface to avoid glare under surgical lights. |
At MFI, we tailor the medical parts finishing process for enhanced surface quality. The significance of enhanced surface quality extends beyond aesthetics. In medical applications, it’s largely about patient safety and device efficacy. Smooth surfaces on medical devices, such as implants and surgical instruments, minimize the risk of complications, making the finishing process a critical step in medical manufacturing.
Our High-Energy Centrifugal Barrel Tumbling Machines are designed to:
- Smooth Critical Surfaces: Ensuring that precision parts such as metal catheter-type tubes have no sharp edges, which is vital when these devices navigate through sensitive areas like blood vessels.
- Remove Machine Lines and Break Sharp Edges: A key aspect of enhancing the surface quality of medical devices, including those with complex geometries.
- Achieve Various Finishes: From high-polish to matte finishes, our machines can accomplish the desired aesthetic and functional qualities without compromising the part’s integrity.
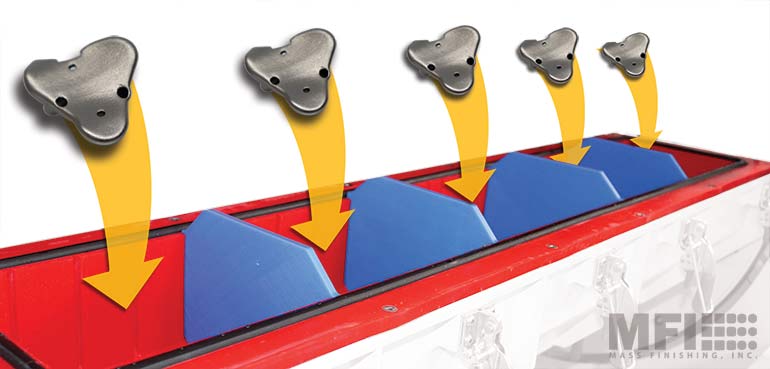
No Part-On-Part Damage
MFI’s HZ-Series machines stand out in their capability to prevent part-on-part damage. Through the use of barrel dividers, operators are able to easily divide and create individual chambers within each barrel, protecting their delicate parts. The dividers are also easily removed or moved to accommodate parts both large and small.
The picture below depicts the different size barrels MFI offers (based on the medical finishing system chosen), as well as the number of dividers that fit within each barrel to create individual process chambers.
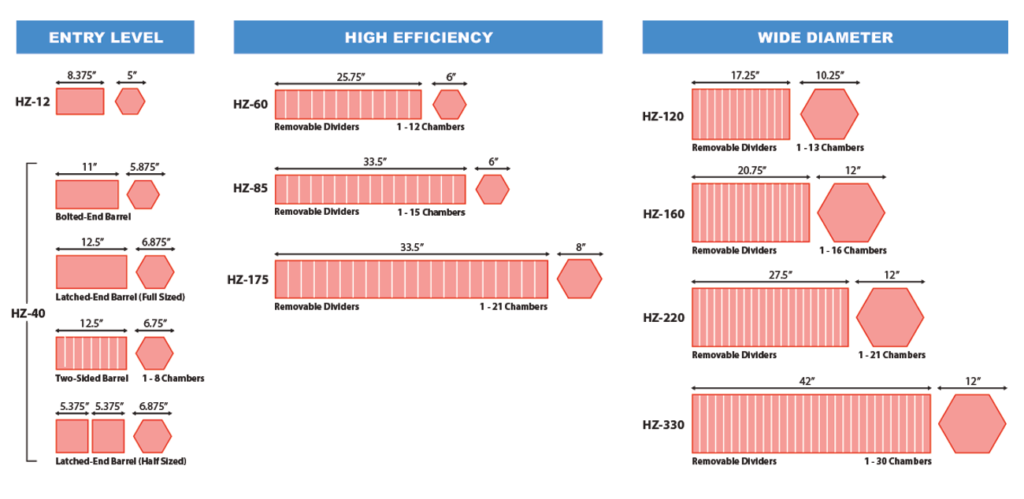
With MFI centrifugal barrel tumblers, the part only needs to fit in the chamber with room to tumble. There is no need to hold the part in place or fixture it to prevent damage.
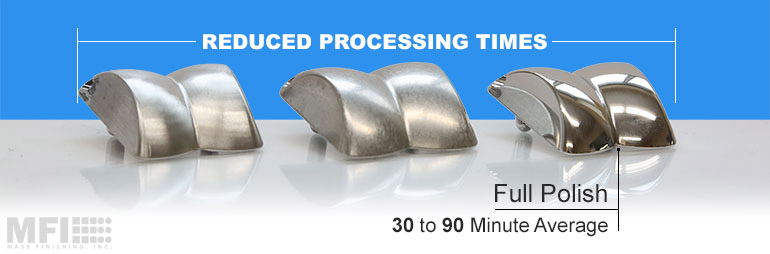
Reduced Processing Times
At MFI, we recognize that time is a crucial factor in the fast-paced medical industry. That’s why our High-Energy Centrifugal Barrel Tumbling Machines are not just about achieving the best finish but also about doing it efficiently. Our equipment is designed to significantly reduce processing times, while maintaining, and often enhancing, the quality of the finish.
One of the most significant advantages of our medical parts finishing systems is the ability to eliminate handwork and allowing customers to implement a process that is efficient and repeatable.
- Automated Finishing Process: Our machines take over the tasks traditionally done by hand, ensuring a consistent and repeatable finish on every part. This consistency is crucial in medical device finishing, where every part must meet stringent quality standards.
- Efficiency and Consistency: By automating the process, we not only speed up production but also eliminate the variability and potential errors associated with hand finishing. This results in a uniformly high-quality finish across all parts.
How MFI Reduces Processing Times
The key to our reduced processing times lies in the high-energy centrifugal force that is created by our tumbling machines. The high-speed motion created by the HZ-Series machines create pressure and friction on the parts, reaching upwards of 12 times the force of gravity (12G).
Unlike traditional vibratory finishing methods, which can take anywhere from 8 to 16 hours, our centrifugal barrel tumblers can accomplish the same tasks in a fraction of that time. This increased speed doesn’t just save time; it also enhances productivity, allowing for more parts to be finished in a given time frame.
Achieving the finish you desire varies greatly by the raw condition of the part. To give you a clearer picture of the efficiency of our systems, let’s look at some average processing times for different finishing stages:
Average Process Times | |
Light Edge Break/Deburr | 5 – 20 minutes |
Rough Grind/Deburr | 20 – 60 minutes |
Full Polish from Raw Part | 30 – 90 minutes |
Note: These times vary depending on the starting surface roughness of the parts.
Mass Finishing uses a combination of tumbling media to first grind and smooth out the surface and then a final step media to add a high shine or polish to parts. Some of the most common media used in the medical industry includes:
- Medical Cob Media: Specially formulated without animal fats, this media is ideal for achieving high-polish finishes on medical devices.
- Ceramics/Plastics: These are primarily used for effective deburring of medical parts.
- Synthetic Media: Chosen by clients who prefer to avoid polymer contact with their parts, synthetic media is also used for deburring.
- Porcelain Media: Particularly suited for polishing smaller parts like bone screws, where precision and delicacy are vital.
Diverse Material Compatibility
Our High-Energy Centrifugal Barrel Tumbling Machines demonstrate remarkable versatility, effectively working with a variety of materials such as Aluminum, Carbon Steel, Stainless Steel, Nitinol, Titanium, Peek, and Acrylic. This extensive material compatibility is essential for meeting the diverse needs of the medical device industry, which uses a variety of materials for different applications.
The secret to our success in material compatibility lies in the adaptability of our systems:
- Customized Media Selection: Our machines can utilize both wet and dry media of various sizes and types. By tailoring the media to each specific application, we ensure that each material is treated with the most effective finishing process.
- Versatile Equipment Design: The same MFI machine is capable of switching between different media types, making it ideal for manufacturers who work with multiple materials. This flexibility allows for seamless transitions between projects without the need for multiple machines.
Our commitment to versatility is not just about handling different materials; it’s about understanding and optimizing the finishing process for each one. Here’s why our systems are ideal for diverse materials:
- Efficient Process Tailoring: We recognize that each material has unique properties and finishing requirements. Our ability to tailor the finishing process, including the selection of the appropriate media, ensures optimal results for every material.
- One-Stop Solution: With MFI’s equipment, manufacturers no longer need separate finishing systems for different materials. Our machines provide a comprehensive solution, making the production process more streamlined and cost-effective.
This broad material compatibility is particularly beneficial in the medical device industry, where manufacturers often work with a range of materials.
Our machines can handle the delicate nature of Nitinol, the robustness of Stainless Steel, and the precision required for Acrylic and Peek components. This versatility not only improves the efficiency of the manufacturing process but also ensures that each material receives the exact finishing it requires for optimal performance and safety in medical applications.
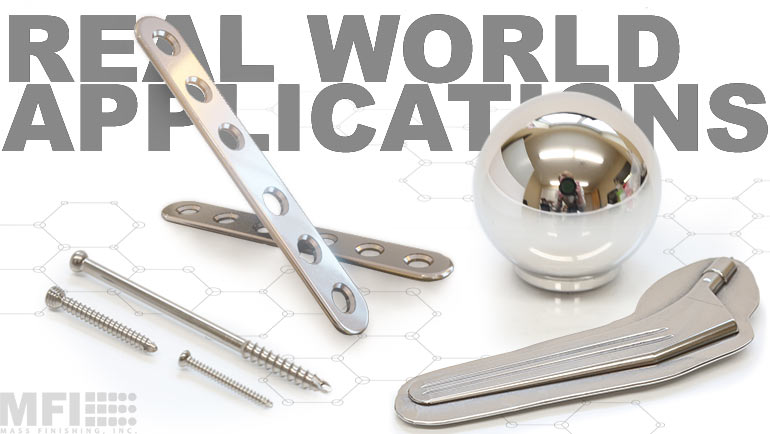
Real-World Applications in Medical Device Finishing
Our medical device polishing and finishing solutions are instrumental across a spectrum of medical applications. From orthopedic implants to needles and blades, our medical finishing systems ensure optimal performance and longevity. We also specialize in finishing acrylic products, such as hearing aids, using our high-energy centrifugal barrel tumbling equipment.
Some of the most common medical parts finished using our HZ-Series centrifugal barrel finishing machines include:
- Medical devices & implants
- Bone plates
- Bone screws
- Surgical tools
- Prosthetics / Orthopedic Implants
- Stents and heart valves
- Needles and blades
- Medical instrumentation
- Acrylic products (such as hearing aids)
Below are some real-world examples of metal finishing for medical applications. All the results shown were achieved with MFI’s centrifugal barrel tumbling systems.
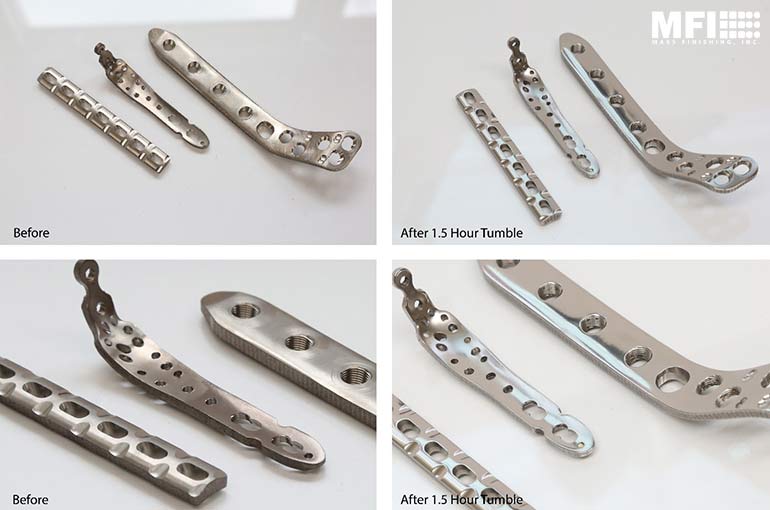
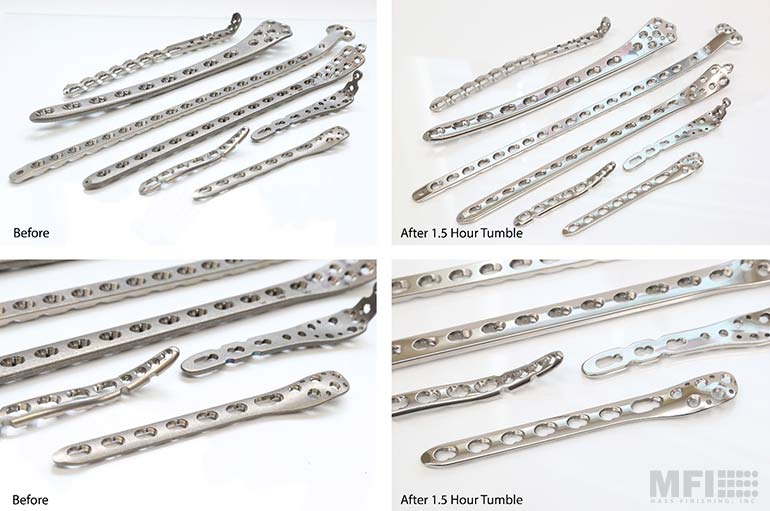
Medical Application 1: Bone Plates
Bone plates are one of the most common medical applications that utilize our HZ-Series machines. These parts sometimes reach 12 to 14 inches in length and would typically fail in centrifugal disc and vibratory finishing machines.
With equipment like our HZ-60 Centrifugal Barrel tumbler, batches of these parts are easily taken from rough machining, casting, or printing and brought within the customer spec.
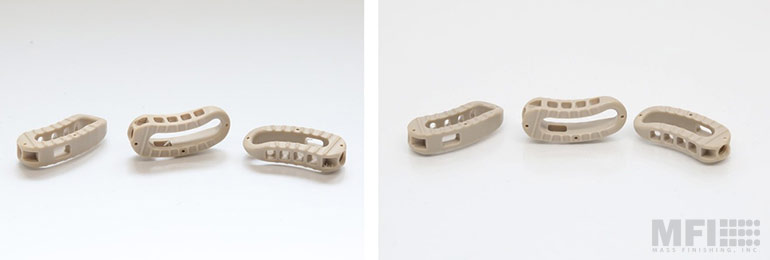
Medical Application 2: PEEK Deburring
This tricky material can be problematic to deburr because of the flexible burrs that are left from machining.
The high g-force of our HZ-series machines can effectively remove sharp edges and cut off flash and burrs left on these parts to make them more manageable to pass quality requirements.
Part Material | PEEK Plastic |
Part Size | 0.25” x 0.75” x 0.5” |
Machine Used | HZ-Series Centrifugal Barrel Tumbler |
The Finishing Process | 1-Step Process: 45 minutes of deburring in ceramic media |
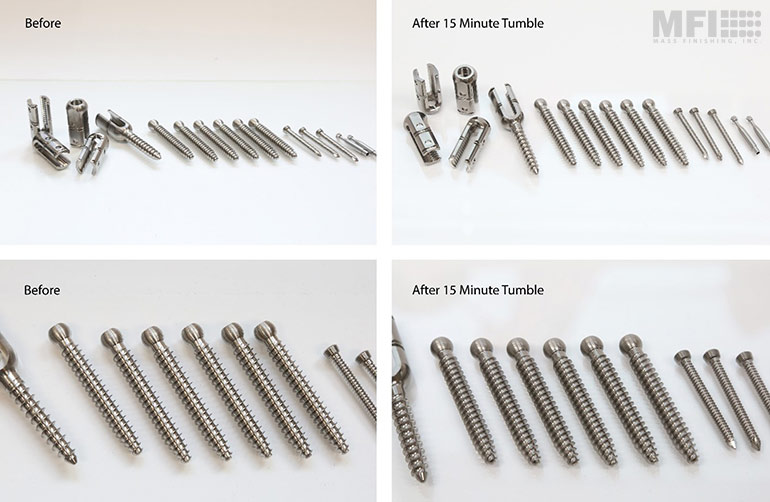
Medical Application 3: Bone Screws & Fasteners
Medical screws and tulips used to fasten bone plates and other apparatus to human bones are often machined. The heads and screw tips are often left with unwanted burrs and unwanted sharp edges from the cutting process.
One step in an HZ-series tumbler can ensure a smooth product on lots of several hundred in a single batch.
Part Material | Titanium |
Part Size | 0.1” x 1.5” x 0.1” |
Machine Used | HZ-Series Centrifugal Barrel Tumbler |
The Finishing Process | 1-Step Process: 15-20 minutes of finishing in non-abrasive porcelain media. |
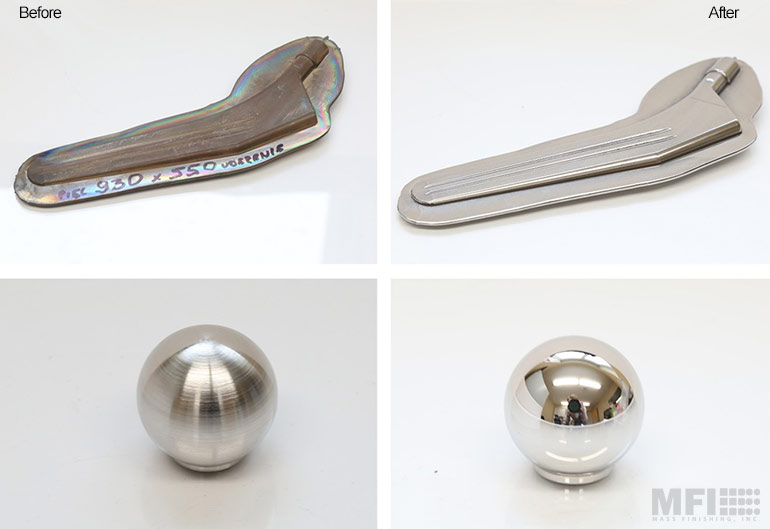
Medical Application 4: Orthopedic Replacements
Orthopedics such as hip, knee, and ankle joint replacement parts are machined and 3D printed.
A three-step process utilizing our HZ-Series machine can take a rough machined, cast, or printed part and bring the Ra to below 2 microinches in some cases using no chemicals or accelerants to corroded the surface material.
Part Material | Cobalt Chrome |
Part Size | 0.25” x 1.25” x 3.75” |
Machine Used | HZ-Series Centrifugal Barrel Tumbler |
The Finishing Process | Step 1: 30 minutes of rough grinding Step 2: 30 minutes of pre-polishing Step 3: 30 minutes of polishing |
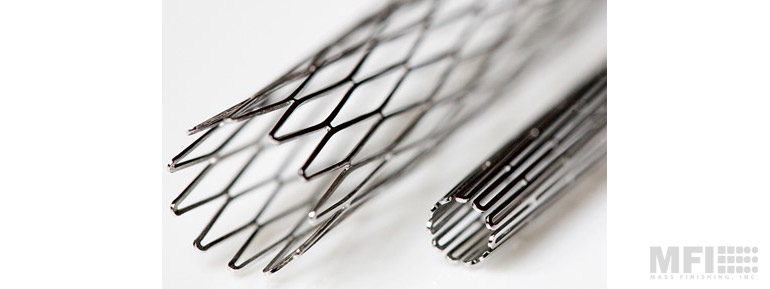
Medical Application 5: Nitinol Wire
This application highlights the aggressive yet gentle nature of the centrifugal barrel tumbling process. Nitinol is known for its “shape-memory” properties and is used in stents and other cardiovascular applications.
The process of laser cutting nitinol wire leaves it with sharp edges and often blue discoloration. MFI’s finishing process can eliminate the hand work involved with preparing these pieces for assembly.
Part Material | Nitinol |
Part Size | 1.5” x 0.25”x 0.25” |
Machine Used | HZ-Series Centrifugal Barrel Tumbler |
The Finishing Process | 1-Step Process: Finishing with abrasive media to remove heat treat scale generated by laser cutting. |
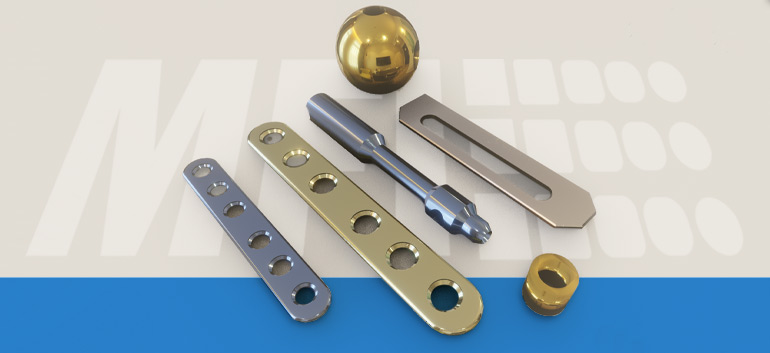
Conclusion: MFI’s Impact in the Medical Industry
At Mass Finishing, Inc., we are dedicated to advancing medical device finishing technology. Our commitment over the last two decades to quality and innovation has made us a leader in medical device polishing and finishing. Our customers value the quality, consistency, and efficiency our machines bring to their manufacturing processes, making us a trusted partner in medical device production.
Are you looking to elevate the standard of your medical device finishing? Connect with our team at Mass Finishing, Inc. to explore how our solutions can enhance your manufacturing processes.
Contact Us Today:
Phone: (320) 543-3222
Email: sales@massfin.com
Take the first step towards optimizing your medical device production with industry-leading expertise and technology. We are here to help you achieve exceptional results.