HZ-60 Centrifugal Barrel Finisher
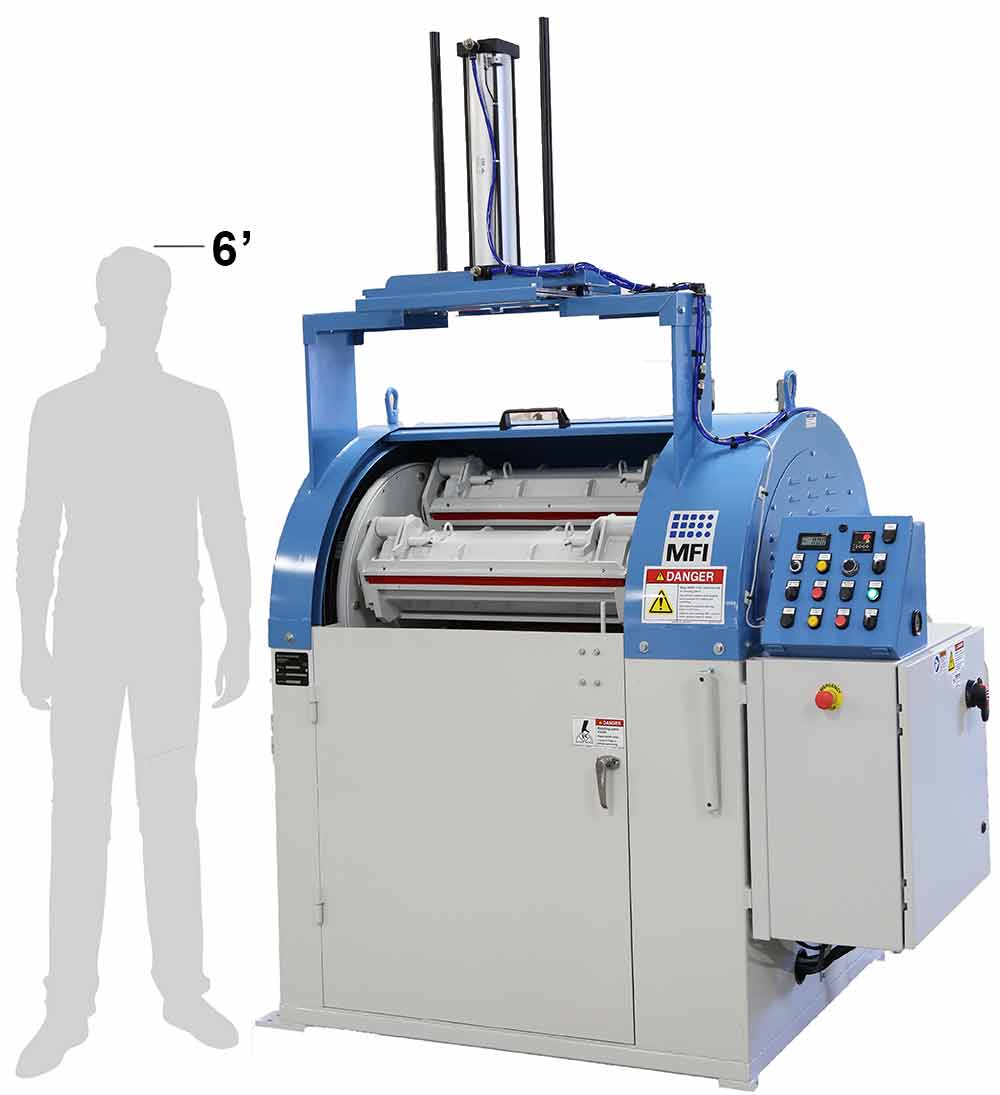
HZ-60 High-Energy Centrifugal Barrel
Finishing Machine
The HZ-60 is a full-sized industrial finishing machine known for its high efficiency. The HZ-60 provides more than double the capacity and efficiency when compared to MFI’s compact centrifugal barrel tumblers like the HZ-12 and HZ-40. Equipped with a cover lift, this model eliminates the need for any heavy lifting.
Machine Type: High Efficiency
Max Part Size: 25.5″ L x 5.25″ D
Barrel Dimensions: 25.75″ L x 5.8″ D
Popular Industries: Automotive & Transportation, Medical
HZ-60 Basic Operation
The HZ-60 Centrifugal Barrel Finishing Machine is a high-energy finishing machine. It uses the pressure and friction created through centrifugal force to quickly remove excess material, polish part surfaces, and create a uniform finish. The finish achieved by the HZ-60 is isotropic, meaning parts are polished uniformly and evenly in all directions, something that cannot be achieved by hand finishing.
With variable frequency control, you can control the speed of the tumble. Manufacturers can achieve a simple polish at low speed or even aggressive deburring and radiusing at higher speeds, reaching up to 225 RPM.
This machine can be fully customized with a touchscreen control panel, parts separator, drain pan, infrared safety curtain, and more. See the accessories table for more information on customizable options.
How It Works
Centrifugal barrel finishing, also known as centrifugal barrel tumbling, operates on the “Ferris Wheel” principle with a one-to-one ratio of barrel rotation to turret rotation. The process involves loading four barrels with a mixture of parts, water, compound, and media, which are filled to around 50-80% capacity. As the machine rotates, the barrels spin around the turret and on their own axis, creating a sliding force inside the barrel.
HZ-60 Features and Benefits
Full-size production
This model provides more than double the capacity and efficiency of MFI’s compact centrifugal barrel tumblers like the HZ-12 and HZ-40.
Long, narrow barrels
At 25.75” in length and just under 6″ wide, these barrels can be divided to create 12 chambers inside each of the 4 barrels. This helps to avoid part-on-part impingement and damage.
Built-in cover lift
Easily lift off your barrel lids, eliminating the need for excessive force when loading and unloading the machine. This feature saves time and promotes safety.
Reduce manual labor
Manual labor can be very time-consuming, expensive, demanding, and dangerous. Our HZ-Series Centrifugal Barrel Finishers take the handwork out of finishing.
Short cycle times
In a matter of minutes, centrifugal barrel finishers can clean up metal, acrylic, rubber, and other materials in what could take hours or even days by hand.
Quieter operation
Compared to vibratory equipment, this series runs much quieter. They can be installed in places you wouldn’t want vibratory machines installed, such as where other machines’ tolerances may be affected.
Achieve a mirror-like finish
Nearly impossible to achieve by hand, our polishing machines can achieve a mirror-like finish on a variety of parts.
Save time and money
Due to the friction and force created by these machines, they run much more efficiently, using less media, water, and compound compared to other finishing methods.
Safe and easy operation
The integral hood switch and two-button jog requirement make this series extremely safe to operate. The hood is securely locked during cycles.
HZ-60 Barrels
The HZ-60 Centrifugal Barrel Finisher features four 25.75” wide barrels. These barrels come with removable lids that are secured with cam locks for safe and efficient operation. The machine is equipped with an air-driven cover lift that is controlled by a toggle switch located on the control panel. This feature allows for easy removal of the barrel covers.
With 11 divider slots, it is possible to create 12 individual chambers within each barrel if utilizing our optional barrel dividers. This allows operators to separate parts into several different chambers within each barrel. This is a critical feature when part-on-part impingement needs to be avoided.
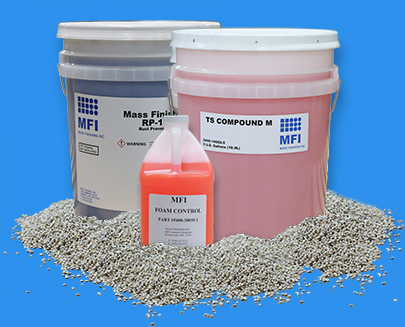
Get Stocked Up on the Essentials
Shop our media and compound store.
HZ-60 Recommended Accessories
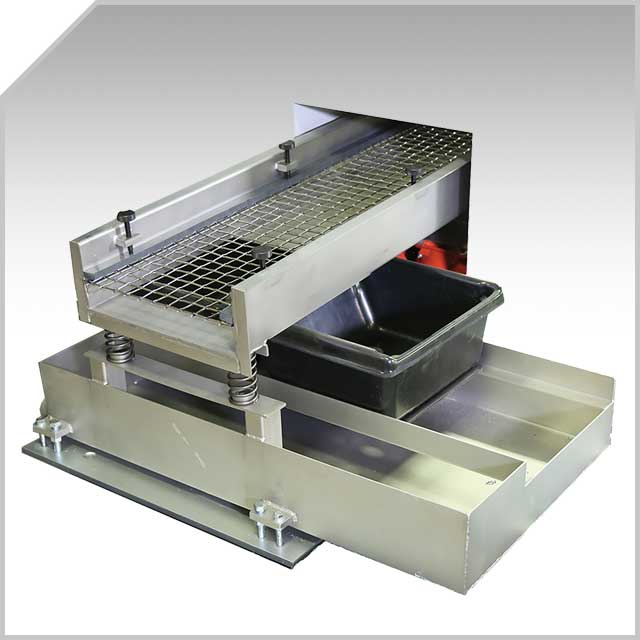
Part & Media Separator
- Simplify the media & part separation process
- Dump fully loaded barrels
- The machine vibrations separate the media & parts out of the machine and into bins
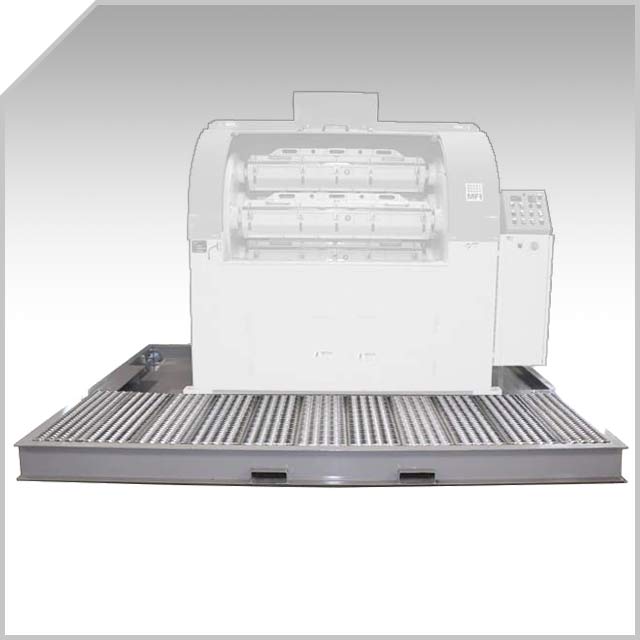
Drain Pan
- Collects water and drainage during the loading/unloading process
- Grip strut floor surface to prevent operator slips and falls
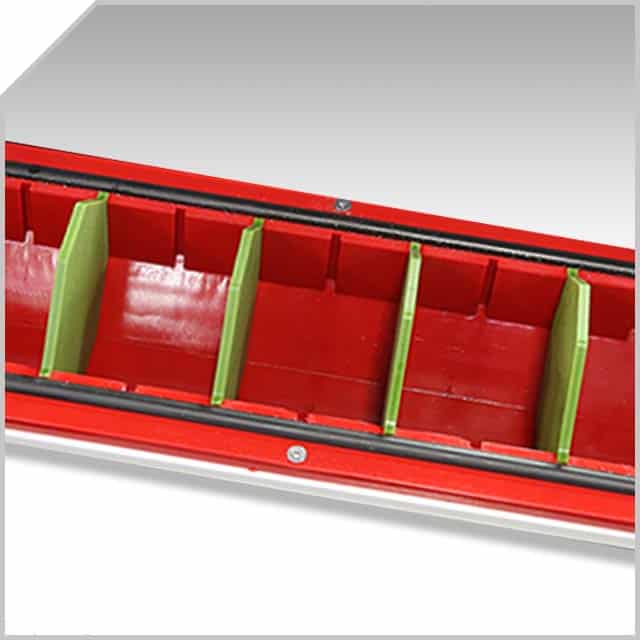
Barrel Dividers
- Create separate chambers inside each of your barrels
- Reduce part-on-part impingement
- Available for all HZ-Series models (except HZ-12)
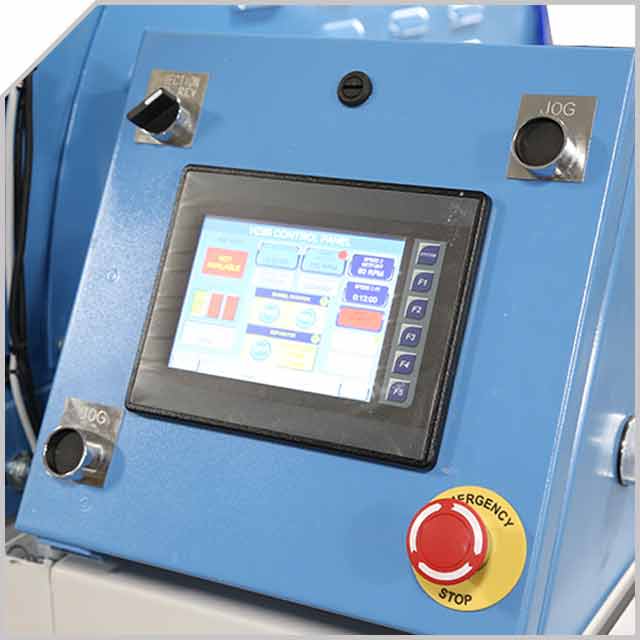
PLC Touchscreen
- Store processes as recipes for easy process selection
- Replaces the analog cycle start buttons
- Allows for better monitoring of machine use and time
Additional HZ-60 Specs & Resources
Main Motor |
|
Barrel Rotation Motor |
|
Machine Voltage |
|
Capacity/Consumables |
|
Approximate Shipping Weight |
|
Overall Dimensions |
|
Machine Construction |
|
Paint |
|
Barrel Construction |
|
Barrel Liners |
|
Barrel Cover Lift |
|
Control Panel |
|
Variable Speed Drive |
|
Brake |
|
Safety Interlock |
|
Vibratory Media Separator |
|
Spray Header for Separator |
|
Drain Pan |
|
Processing Table and Sludge Tank |
|
Barrel Dividers |
|
PLC Controller |
|
Rinse Screen |
|
Infrared Safety Light Curtains |
|
Light Tower Indicator |
|
Media Return System |
|
Custom Logo/Paint |
|
Centrifuge Module – CF55 SD Series MicroseparatorTM |
|
Automatic Door Opener |
|
Media/Compound |
|
Media Storage Rack |
|
Are You Interested in the HZ-60?