Ever wondered how cutting-edge industries achieve those impeccably smooth surfaces? It’s all about the magic of isotropic finishing.
This guide peels back the layers of the isotropic finishing process, revealing how it’s transforming everything from aerospace components to medical devices. You’ll learn the stark differences between isotropic and traditional directional finishing. This will help you uncover the benefits isotropic finishing provides and explore the diverse equipment and processes used to achieve this technique.
By the end of this read, not only will you grasp the intricate workings of isotropic finishing, but you’ll also understand why it’s becoming the go-to solution for industries prioritizing precision and durability. So, let’s dive in!
What is isotropic finishing?
Isotropic finishing is a process that creates a uniformly smooth and non-directional surface finish on parts, significantly enhancing their quality and performance.
Unlike traditional finishing methods, which often leave directional textures, isotropic finishing ensures uniformity in all directions. You can achieve it through a variety of finishing techniques that evenly impact the component’s surface. This results in a part that is smooth and consistent in all directions.
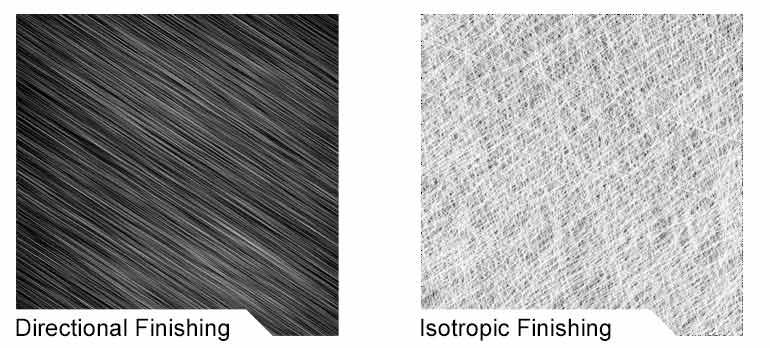
Isotropic vs. Directional Finishing
Traditional finishing methods such as wheel grinding, sanding, or polishing leave behind directional lines and patterns on the surface of a part. These are essentially microscopic grooves and ridges that run in a single direction and are a result of the abrasive action of moving in a consistent pattern.
While traditional finishing methods can be effective for certain applications, the directional texture these finishing methods create can often lead to uneven wear, stress concentrations, and less aesthetic appeal (especially in visible components).
In contrast, isotropic surface finishing creates a uniformly smooth surface with no directional lines. The result is a part that is smooth and consistent in all directions, resembling a uniformly etched, or frosted appearance at a microscopic level.
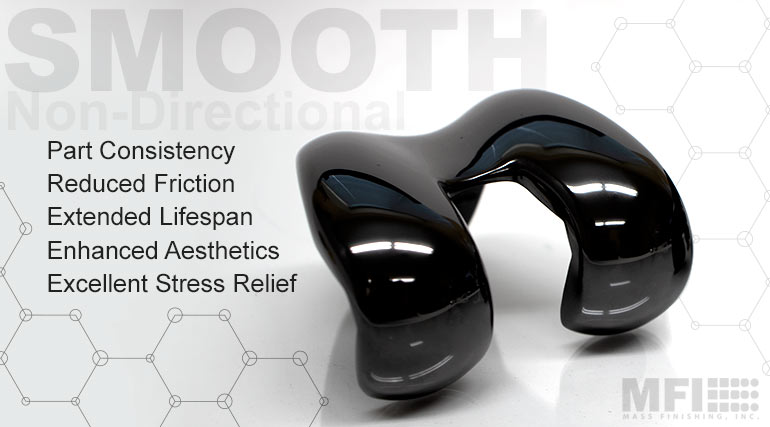
Benefits & Advantages of Isotropic Surface Finishing
Isotropic surface finishing is a sophisticated process that greatly enhances the quality, functionality, and performance of various components.
Some of the key benefits of isotropic surface finishing include:
- Part consistency
- Enhanced part aesthetics
- Excellent stress relief
- Reduced friction
- Extended component lifespan
Part Consistency
One of the standout advantages of isotropic finishing is the consistency it brings to parts finishing.
Unlike traditional finishing methods (wheel grinding, sanding, and polishing) that create a directional finish on parts, the isotropic finishing process ensures uniformity in all directions. This uniformity is crucial in applications where precision and consistency are paramount. This makes isotropic finishing a preferred choice for the medical, aerospace, and automotive industries.
Enhanced Part Aesthetics
Another key benefit of isotropic finishing is enhanced part aesthetics. Isotropic finishing not only ensures uniform smoothness across the entire surface of the part but also elevates the overall appearance compared to machined or hand-finished parts.
The aesthetics of parts processed with isotropic finishing methods are often superior due to the consistent and refined surface texture it provides. Machining or hand finishing can leave marks or inconsistencies. isotropic finishing offers a more uniform and aesthetically pleasing surface. This is especially important in applications where visual appeal is as important as functional performance.
Many people often think that an isotropic finish is synonymous with a high-polish or mirror-like finish. This isn’t necessarily the case. Although it’s common for a variety of industries to require a mirror or high-polish finish on their parts, not all parts with an isotropic surface finish have a mirror-like finish.
Parts with an isotropic surface finish can also have an etched or frosted appearance. What remains constant among parts that undergo an isotropic finishing process, is that each part is uniformly smooth across the entire surface of the part.
Excellent Stress Relief
The non-directional nature of isotropic finishing not only enhances the aesthetic quality but also contributes to the functional performance of the parts.
An isotropic finish reduces the likelihood of stress concentrations, which can lead to material fatigue and failure. It also exposes any surface cracks, allowing parts to flex and relieve internal tensions, making parts less prone to breaking, and therefore enhancing their reliability and safety.
Example: A notable example of reduced surface stress can be found in the following MFI customer application for spring-assist knives. The springs used to help the knives snap open were prone to breaking. After undergoing isotropic finishing through centrifugal barrel tumbling, the stress in the spring was relieved, resulting in a marked reduction in breakage and enhancing the knives’ reliability and longevity. |
Reduced Friction
Another benefit that isotropic finishing contributes to the functional performance of the parts is the reduction of friction between components.
Because of non-directional finish, the microscopic peaks and valleys on the surface of parts are smoothed out. This minimizes the friction between moving components, reducing wear and tear.
Example 1: In the Aerospace Industry, achieving an isotropic finish is extremely important for their critical parts. Airlines have begun remanufacturing their engines and repolishing their blades through the use of isotropic finishing methods such as centrifugal barrel finishing to further reduce the friction on their parts, making them more efficient. Example 2: Engine manufacturers for NASCAR have been utilizing isotropic finishing methods to increase their horsepower. By creating an isotropic finish on their crank shafts, the oil has a harder time sticking to the components and sheds off easier. |
Extended Component Lifespan
The consistent surface texture achieved with isotropic finishing ensures more predictable and uniform wear patterns, extending the lifespan of the component.
For example: Creating an isotropic finish on additive parts is highly sought after by those in the Additive and 3D Printing industry due to its ability to strengthen the parts. Additive parts are known to have a lot more stress in them and require a baking process as well as additional stress relief to make them useable. By creating an isotropic finish on these parts, we’re able to extend their lifespan. |
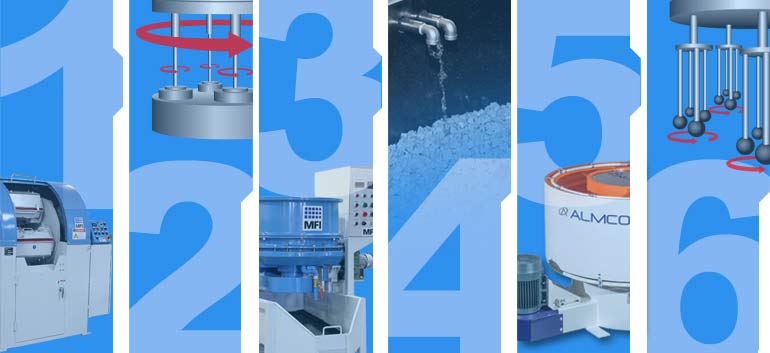
Isotropic Finishing Equipment: 6 Main Finishing Methods
The isotropic finishing process varies depending on the specific finishing method used. There is a variety of isotropic finishing equipment within the industrial finishing industry that can achieve an isotropic finish.
Some examples of isotropic finishing equipment include:
- Centrifugal Barrel Tumbling Equipment
- Centrifugal Disc Finishing Equipment
- Vibratory Finishing Equipment
- Accelerated Surface Finishing / Superfinishing Equipment
- Drag Finishing Equipment
- Lapping Equipment
Each type of equipment has a different finishing process, as well as its own pros and cons regarding cost, processing time, labor intensity, and environmental considerations.
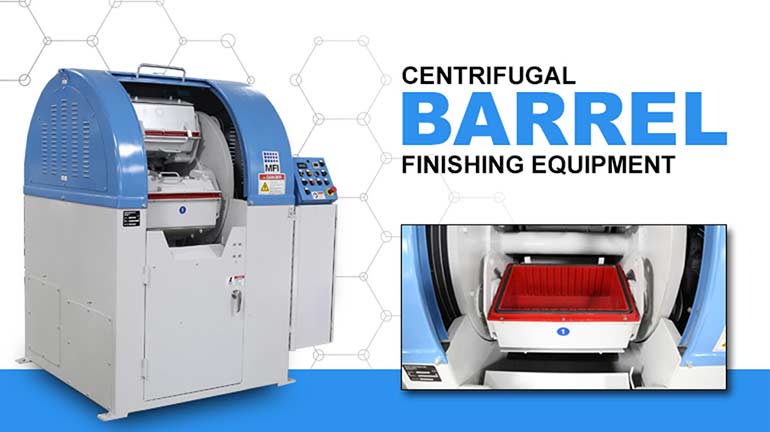
1. Centrifugal Barrel Tumbling Equipment
Centrifugal barrel tumbling is a type of isotropic finishing process that utilizes centrifugal force to subject parts and media to pressures greater than the force of gravity. Centrifugal Barrel Finishing Machines (CBF) use this pressure and friction to quickly remove excess material, polish part surfaces, and create a uniform finish. Some machines can reach upwards to 12 times the force of gravity (12G).
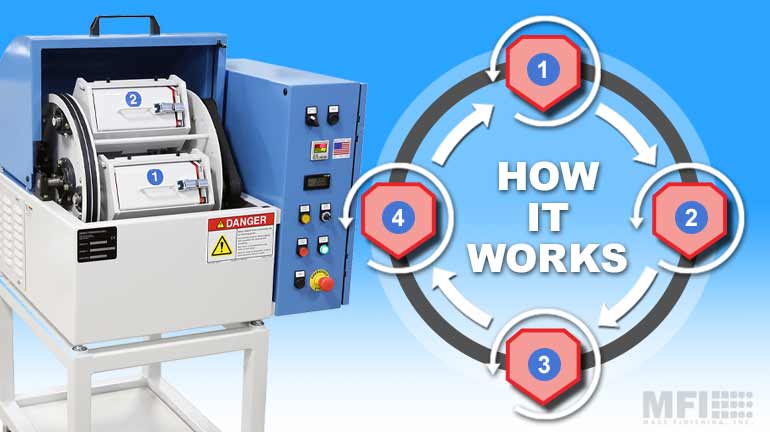
Isotropic Finishing Process: Centrifugal Barrel Tumbling
Centrifugal barrel tumbling typically involves the following steps:
- Step 1: The process involves loading four hexagon-shaped barrels with a mixture of parts, water, compound, and media. The barrels are then locked, and the machine cycle time and speed are set.
- Step 2: As the machine rotates, the barrels spin around the turret in a planetary motion at high speeds. This creates a sliding force inside the barrel. This motion generates high levels of friction and pressure between the abrasive media and parts and causes them to contact each other in random or isotropic directions.
- Step 3: Depending on the finish required, Step 1-2 are repeated with a variety of media and compounds. This allows operators to create a tailored finish on the component(s).
The result is an efficient process that removes burrs, polishes surfaces, and produces uniform finishes that are consistent across the entire part surface.
Centrifugal Barrel Tumbling Pros & Cons
Centrifugal barrel tumblers are known as “high-energy” machines due to the high pressures of gravitational force used. This results in shorter processing times and consistent results. These machines can achieve a smoother surface finish in a fraction of the time compared to vibratory finishing and other methods.
Centrifugal barrel finishing machines are very customizable. Operators can create a variety of isotropic and aesthetic finishes on components, from an etched and frosted finish to a high-polish and mirror-like shine.
Pros:
- Speed of Processing: Capable of quick finishing, especially suitable for small to medium-sized parts.
- Environmentally Friendly: Requires no harsh chemicals to achieve an isotropic finish
- Customizable & Repeatable Process: This process is highly repeatable and is easily customizable depending on your product specifications and requirements.
Cons:
- Cost: Higher initial investment required for equipment.
- Size Limitation: Not ideal for processing parts bigger than 11” diameter.
- Difficult to Automate: Manual Labor is required to load and unload the machines.
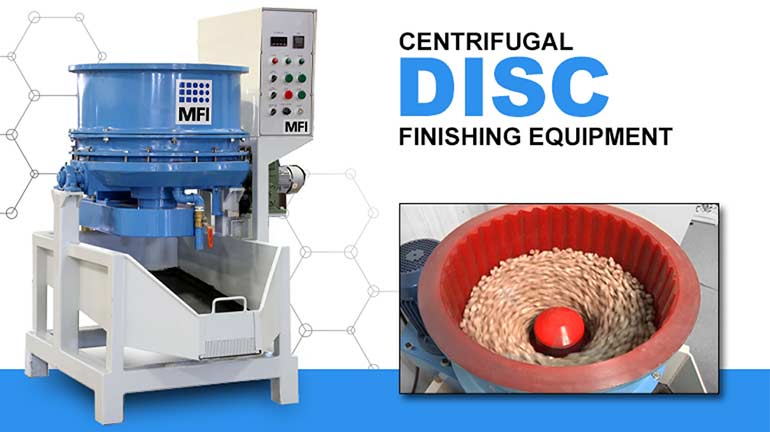
2. Centrifugal Disc Finishing Equipment
Similar to centrifugal barrel tumbling, centrifugal disc finishing is a type of isotropic finishing process that utilizes centrifugal force to subject parts and media to pressures greater than the force of gravity through the use of a rotating disc. Centrifugal Disc Finishers use this pressure and friction to quickly remove excess material, polish part surfaces, and create a uniform finish. These machines are slightly slower than centrifugal barrel tumblers, however, they reach speeds 10 to 20 times faster than vibratory finishing machines.
Isotropic Finishing Process: Centrifugal Disc Finishing
Centrifugal disc finishing typically involves the following steps:
- Step 1: The process involves loading the stationary barrel with a mixture of parts, water, compound, and media. Once setup is complete, the machine cycle time and speed are set.
- Step 2: The disc at the base of the barrel is activated to spin. The spinning motion causes the media and parts to rise and rub against the stationary polyurethane wall of the barrel in a continuous rolling and flowing motion. This action generates consistent contact between parts and media, creating an even, isotropic finish.
- Step 3: Depending on the finish required, Step 1-2 are repeated with a variety of media and compounds to create a tailored finish on the component(s).
Centrifugal Disc Finishers are also available in an automated version, where the loading, unloading, and media separation are managed through a touchscreen PLC interface for continuous and efficient operation.
Centrifugal Disc Finishing Pros & Cons
Centrifugal Disc Finishing presents a viable option for quick processing of small to medium-sized parts, though it’s slightly slower than barrel finishing. Its potential for automation enhances efficiency. However, it does have downsides, such as the risk of part-on-part damage and high water and compound usage, notably exceeding other methods.
Pros:
- Speed of Processing: Capable of quick finishing, especially suitable for small to medium-sized parts (slightly slower than centrifugal barrel finishing).
- Automation Available: Loading, unloading, and media separation can all be managed through a touchscreen interface (with select models).
- Environmentally Friendly: Requires no harsh chemicals to achieve an isotropic finish.
Cons:
- Part Impingement: Prone to part-on-part damage
- High Water and Compound Usage: Water usage is much higher in comparison to other isotropic finishing processes, using approximately 5+ gallons cu ft/hr vs. 1 gallon cu ft/hr for a vibratory machine.
- Size Limitation: Not ideal for processing long parts or parts bigger than 11” diameter.
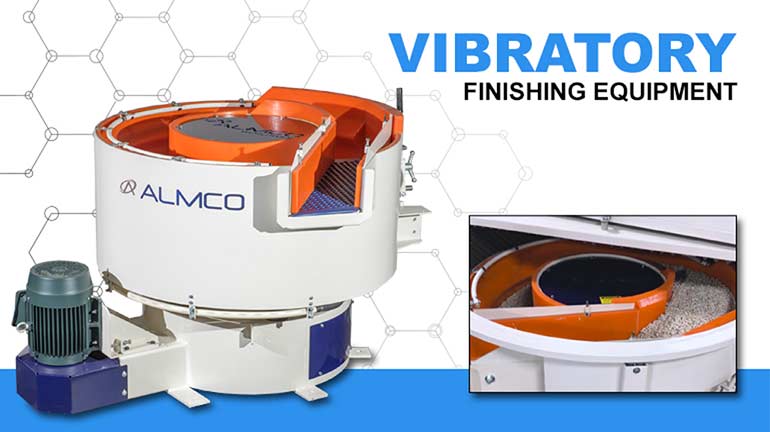
3. Vibratory Finishing Equipment
Vibratory finishing involves using a vibratory machine, such as a vibratory tub or bowl in tandem with abrasive media and chemical compound to achieve a non-directional/isotropic finish on parts.
Isotropic Finishing Process: Vibratory Finishing
Vibratory finishing typically involves the following steps:
- Step 1: Components, water, and abrasive media are placed into a vibratory tub or bowl. The vibratory action of the machine causes millions of small collisions between the parts and media, resulting in the consistent removal of material along part edges and corners.
- Step 2: A mixture of water and finishing compound is then typically used to wash away residual particles and cleaning solutions.
- Step 3: The components are removed by hand or automated process via through-feed systems, conveyors, or by robot.
Vibratory Finishing Pros & Cons
Vibratory finishing is known as a low-energy method for achieving an isotropic finish, as the process often requires longer cycle times due to the less-abrasive nature of the process. This process can take hours, or even days, depending on the surface finish required. However, vibratory finishing equipment is very versatile, and its gentle finishing action poses less risk for damaging delicate parts.
Pros:
- Versatility: Suitable for a broad range of part sizes and types.
- Gentle Processing: Less risk of damaging delicate parts.
- Ease of Use: Generally simpler to operate, requiring less skilled labor.
Cons:
- Longer Processing Time: May take more time to achieve desired finishes compared to other methods.
- Higher Water and Compound Usage: Water usage is typically higher in comparison to other isotropic finishing processes (excluding centrifugal disc finishing).
- Higher Energy Consumption: Due to the extended length of processing time in comparison to other methods (hours/days vs. minutes/hours), this process often has higher operational costs to achieve the same results as other methods.
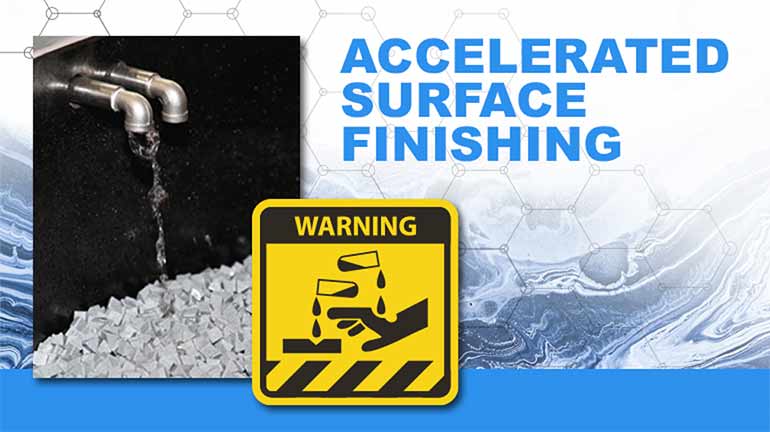
4. Accelerated Surface Finishing / Superfinishing Equipment
Superfinishing is a chemically accelerated surface finishing (CASF) and polishing technique that produces surfaces with an isotropic surface finish. Similarly to vibratory finishing, this isotropic finishing process utilizes vibratory equipment, but additionally relies on acid and caustic chemical compounds to create a chemically accelerated surface finish on parts.
Isotropic Finishing Process: Accelerated Finishing / Superfinishing
Isotropic superfinishing is achieved in a two-stage process:
- Stage 1: Refinement – Metal parts are placed in a vibratory bowl along with ceramic media and a chemical additive. The vibratory action triggers a chemical reaction between the metal surface and the ceramic, forming a “conversion coating” on the metal. This coating is mechanically soft, making it easy to remove.
- Stage 2: Burnishing – This step involves polishing the metal using non-abrasive finishing media within the vibratory equipment. The parts are submerged in this media, and the soft conversion coating is gently rubbed off, smoothing the surface.
Throughout the process, the chemical compound acts as a catalyst, reducing the energy needed for material removal and controlling the speed of refinement.
Accelerated Finishing / Superfinishing Pros & Cons
Accelerated finishing is known for delivering high-quality, precision finishes, especially on complex component surfaces. Its accelerated process, facilitated by the use of additional chemicals, offers an advantage over traditional vibratory methods. Despite these benefits, it demands skilled labor for effective operation and handling, and raises concerns about safety and environmental impact due to the caustic chemicals utilized in the process.
Pros:
- High-Quality and Precision Finish: Achieves extremely high-quality finishes, ideal for precision applications. Ability to finish recessed and none line-of-sight component surfaces
- Accelerated Finishing: In comparison to vibratory finishing methods, this process is accelerated due to the additional chemicals that are used, eroding the surface of the component.
Cons:
- Cost: This process has a higher cost due to specialized equipment and process.
- Harsh Chemicals: Involves the use of caustic chemicals, raising environmental and safety concerns. Chemicals have to be neutralized before they can be disposed of.
- Skilled Labor Needed: Requires more skilled operation and handling.
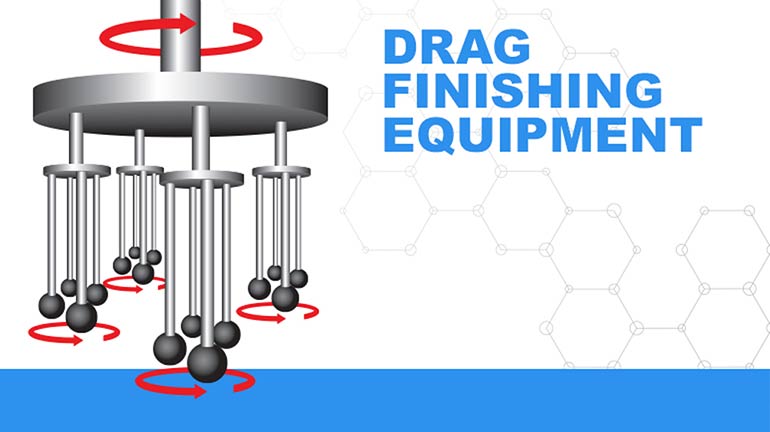
5. Drag Finishing Equipment
Drag finishing is a high-precision surface finishing process where components are securely clamped in holders and dragged through a media-filled drum at high speeds. This method generates intense contact pressure between the component and the media, rapidly producing high-quality finishes such as edge rounding, smoothing, or mirror polishing. Unique to drag finishing is the individual treatment of each part, avoiding any part-on-part contact, making it ideal for delicate or high-value components.
Isotropic Finishing Process: Drag Finishing
Electropolishing is achieved in 3 distinct stages:
- Stage 1: Clamping the Parts – The components are firmly clamped onto a carousel of specially designed fixtures/holders. The carousel is typically equipped with 4-12 holders.
- Stage 2: Movement and Dragging – Once the machine is activated, a motor moves the carousel in a circular motion. This movement drags the parts through the bowl or tub.
- Stage 3: High-Speed Contact and Finishing – The fixtures and parts move at high speed, creating substantial contact pressure and friction between the components and the media. This interaction, coupled with the friction generated, leads to high-precision edge rounding, smoothing, or even achieving a mirror finish.
Drag Finishing Pros & Cons
Drag Finishing is known for its efficiency and the ability to customize for specific part types. It is particularly beneficial for delicate parts, as it avoids part-on-part contact. However, the process entails a higher initial investment in equipment and increased operational expenses.
Pros:
- Efficient: The drag finishing process yields results in a short amount of time.
- Customizable: You can tailor it for specific part types.
- Safe for Delicate Parts: No part-on-part contact or friction among workpieces, preserving part quality.
Cons:
- Cost: Higher initial investment required for equipment, as well as higher operational expenses.
- Energy Intensive: Consumes a significant amount of energy.
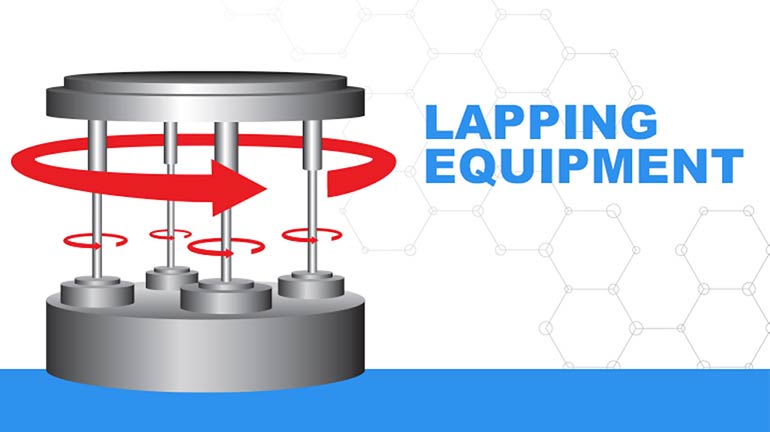
6. Lapping Equipment
Lapping is a finishing technique that uses a methodical, abrasive action via a flat lapping plate and an abrasive slurry to remove material from the surface of a component. This isotropic finishing process precisely smooths and flattens the surface of the component, achieving a high level of accuracy and smoothness.
Isotropic Finishing Process: Lapping
Lapping typically involves the following steps:
- Step 1: The component being finished is placed against a lapping plate.
- Step 2: The lapping plate is coated with a lapping slurry and moves beneath the rotating component, creating contact with the component’s surface.
- Step 3: Through a combination of the abrasive slurry and the movement of the component against the plate, material is gradually removed from the component’s surface.
Initially, material is removed for flatness, followed by refining the surface to a specific roughness average (Ra), if required.
Lapping Pros & Cons
Lapping is known for achieving excellent flatness and surface finishes across various materials. However, it is a labor-intensive process, requiring skilled operators. It is also inherently slow, particularly when very fine finishes are required, and demands regular maintenance, including the replacement of lapping plates and abrasives.
Pros:
- Precision Finishing: Capable of achieving high levels of flatness and surface finish.
- Material Flexibility: Applicable to a wide range of materials.
- Control over Finish: Enables fine control of the surface finish.
Cons:
- Labor Intensity: More labor-intensive and requires skilled operators.
- Slow Process: Takes longer, especially for achieving very fine finishes.
- Equipment Maintenance: Requires regular upkeep and replacement of consumables like lapping plates and abrasives.
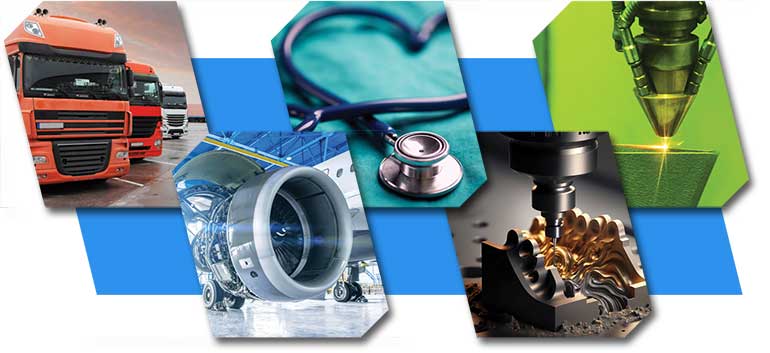
The Importance of Isotropic Finishing Across Industries
Isotropic finishing plays a crucial role in various industries, offering significant benefits in terms of quality, performance, and reliability. This specialized finishing technique achieves an even, non-directional surface. This is vital in fields demanding high precision and stringent quality standards. Its impact is particularly notable in the medical, aerospace, and automotive sectors.
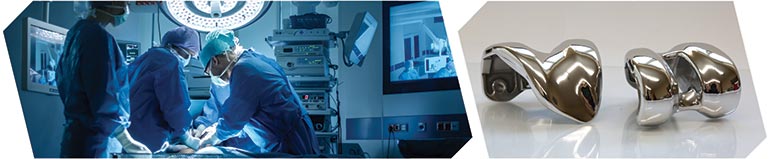
Isotropic Finishing in the Medical Industry
The medical sector greatly benefits from isotropic finishing. It ensures consistent and high-quality surfaces on complex medical devices and implants. This level of finish is critical in reducing the risk of complications post-surgery by minimizing plaque buildup on medical devices like implants, plates, and screws. Additionally, the efficiency of isotropic finishing methods accelerates the processing of medical parts, a crucial factor in the fast-paced medical environment.
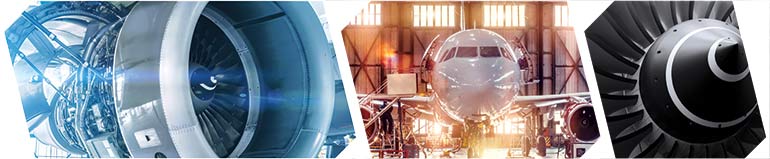
Isotropic Finishing in the Aerospace Industry
In the aerospace industry, isotropic finishing is pivotal for achieving the precision and reliability required in aerospace components, from jet engine blades to intricate airplane parts. This finishing method not only provides the necessary quality but also eliminates manual labor. This enables a more efficient and repeatable process. Such precision and efficiency are indispensable in the aerospace industry, where every detail has a significant impact on overall safety and performance.
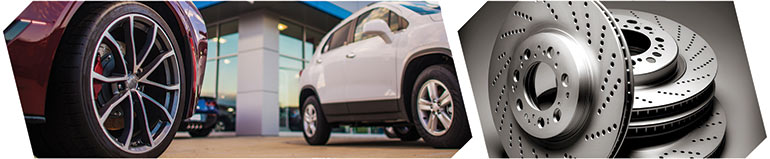
Isotropic Finishing in the Automotive Industry
For the automotive sector, especially in high-performance and racing domains, isotropic finishing plays a crucial role in enhancing engine efficiency and vehicle performance. Engine components that have undergone isotropic finishing shed oil more efficiently, which reduces friction and heat. This, in turn, leads to increased horsepower and improved engine performance.
Each sector derives unique benefits from isotropic finishing, highlighting its versatility and essential role in modern manufacturing and engineering processes. This finishing method not only ensures the highest quality standards but also contributes to the enhanced performance and longevity of the products in these demanding industries.
Conclusion
From detailed aerospace parts to crucial medical devices, isotropic finishing is a key player in achieving top-quality results in industrial manufacturing. Throughout this guide, we’ve explored the stark contrast between isotropic and traditional directional finishing. We’ve also understood how isotropic finishing leads to uniform, non-directional surfaces that enhance both component function and form.
In addition, we’ve explored the benefits of isotropic finishing, including stress relief, reduced friction, and increased durability, underscoring its significance in prolonging component life. Through a detailed look at various isotropic finishing techniques, we’ve gained a comprehensive view of each isotropic finishing process, as well as their pros and cons.
Professionals and enthusiasts can appreciate the significant role it plays in modern manufacturing by understanding the nuances and benefits of isotropic finishing. Thus, they can become better positioned to leverage the full potential of isotropic finishing, tailoring its application to optimize their manufacturing processes and product performance.